JC Casting is a Professional stainless steel valve casting company.Such as material of 316L ,304L.Duplex 2205.As a leading investment casting foundry in the valve industry. JC Casting has its own independent factory and advanced CNC machine equipment. We have been providing customers with high-quality stainless steel valve products for 20 years.
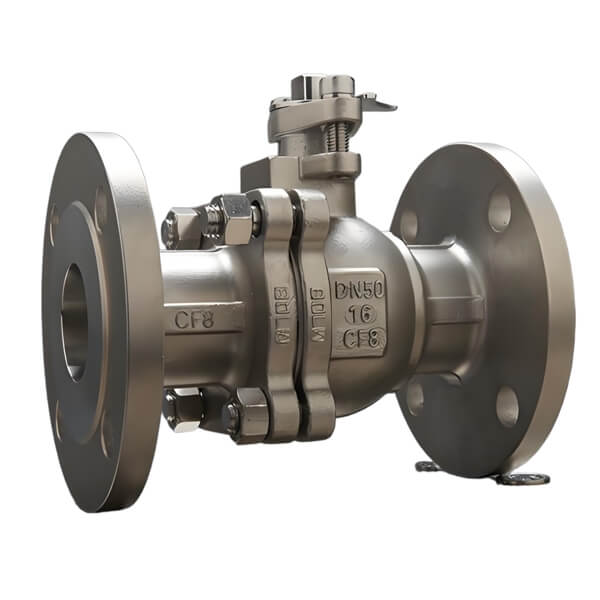
Advantages of stainless steel valve casting
Stainless steel valve casting has the following significant advantages:
- Excellent corrosion resistance: 316L stainless steel contains molybdenum. Significantly improved resistance to chlorides and other corrosive media
- High strength and durability: The cast valve structure is sturdy. Long service life
- Good sealing performance: Precision casting ensures high precision of valve sealing surface. Low leakage rate
- Wide range of applications: Applicable to many industries. Such as petroleum, chemical, pharmaceutical, food processing, etc.
- Beautiful surface treatment: Stainless steel is easy to polish. Meet high cleanliness requirements
JC Casting Stainless steel Valve Product Range
1. Stainless steel exhaust valve
Designed for pipe systems. Can effectively remove accumulated air. Prevent air blocking. Ensure efficient operation of the system. Adopts precision casting process. Excellent sealing performance.
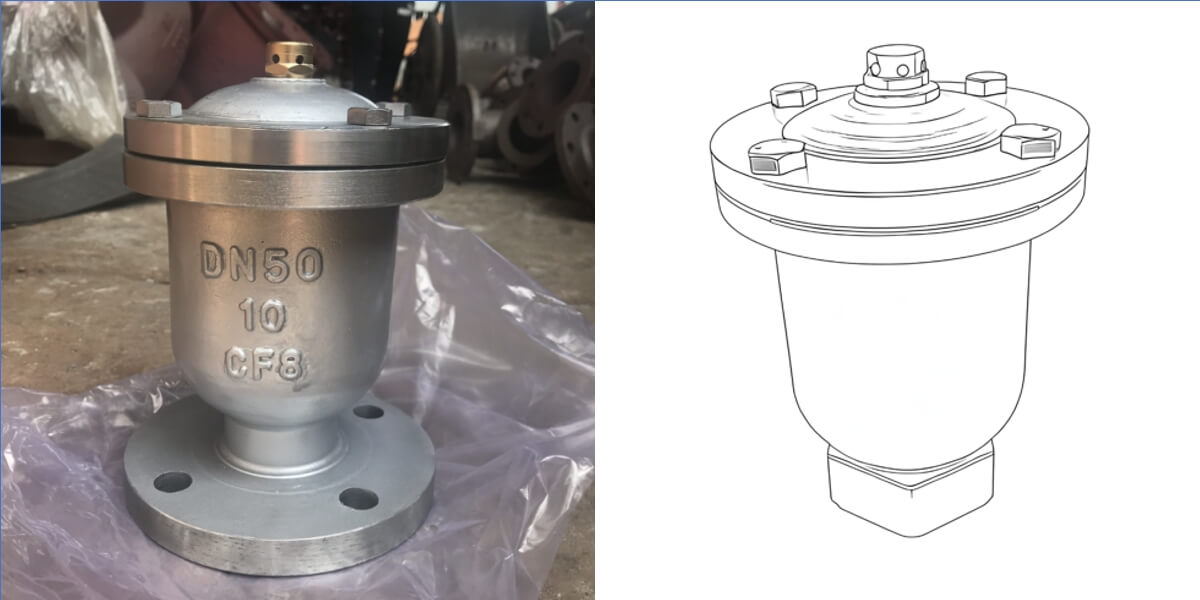

2. Stainless steel knife gate valve
Specially designed for handling media containing solid particles. The knife-shaped gate can cut off fibers and viscous substances. Widely used in sewage treatment, papermaking and other industries.
3. Stainless steel precision casting threaded gate valve
A threaded gate valve made by precision casting. Compact structure. Easy to install. Suitable for small and medium diameter pipeline systems
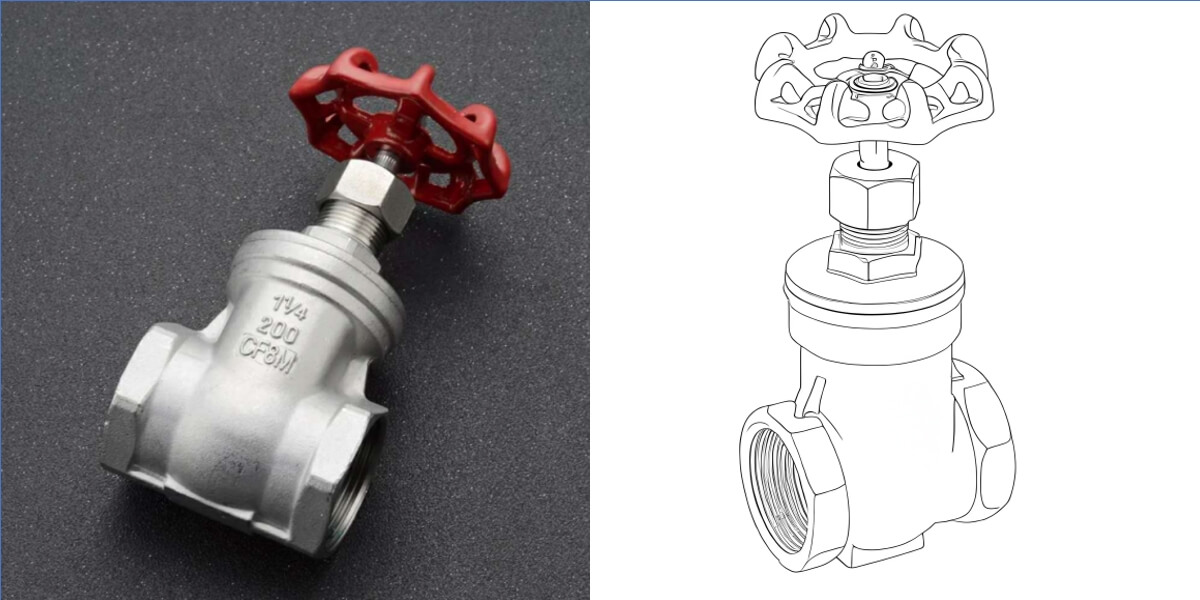

4. Stainless steel butterfly valve
Lightweight design with stainless steel material. It has the characteristics of small flow resistance and fast opening and closing. It is an ideal choice for large diameter pipeline flow control.
5. Precision casting stainless steel check valve
Can automatically prevent medium backflow. Protect system safety. Precision cast valve disc ensures reliable sealing. Suitable for various harsh working conditions.
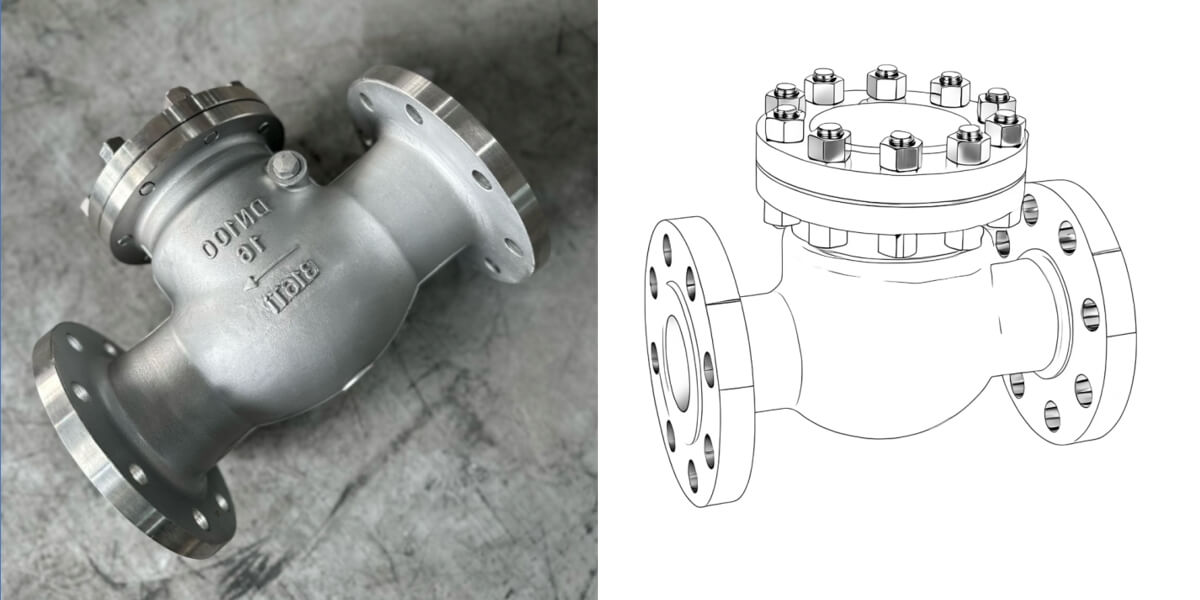
Stainless Steel Valve Casting Production Capacity
JC has comprehensive stainless steel valve casting production capacity:
1–Size range: We can produce valve products of various specifications from DN15 to DN1200.
2–Material selection: Besides standard 316L stainless steel. We can also provide 304, 304L, 316, duplex steel and other materials.
3–Advanced technology:
- – Precision casting (lost wax casting)
- – Sand casting
- – CNC machine tool precision machining
- – Automated surface treatment
4–Quality control: Equipped with spectrometer. X-ray flaw detection and other testing equipment to ensure product quality
5–Export experience: Annual export volume exceeds 20 million US dollars. Products are exported to more than 50 countries and regions. Including Europe, America, the Middle East, and Southeast Asia.
6–Market application: Our valve products are widely used in many industries. Such as petrochemical, power, shipbuilding, water treatment, food and medicine.
Customized service
With 20 years of professional stainless steel valve casting production experience. JC Casting can provide a full range of customized services:
- – Design and production of non-standard valves
- – Special material requirements
- – Personalized surface treatment
- – Special connection methods
- – Brand logo customization
Valve Investment Castings Foundry
At Valve Investment Mold Casting Plant, our advantages set us apart in the stainless steel valve casting industry. We have an exclusive stand-alone factory and state-of-the-art CNC machine tool equipment. This ensures precision and efficiency in every aspect of production. Backed by a team of experienced engineers. Ready to provide customized solutions for your specific needs.
We have full production capacity. Covering a wide range of sizes from DN15 to DN1200. A wide selection of high quality materials.
Our advanced casting and machining technology. Combined with stringent quality control measures such as the use of spectrometers and X-ray flaw detection. Ensure that each valve meets the highest industry standards.