JC Casting is a global Zinc, Magnesium & Aluminium Die Casting Company and Manufacturer.Our engineers can help design solutions and parts specifically for mass production. For die casting parts with requirements of esthetical, functional, or protective coatings. We offer surface finishing. Including powder coating, e-coating, shot blasting, chrome plating, and bright finish.
What Is Die Casting?
Die casting is a type of metal casting process. Under high pressure, It forces molten metal into a mold cavity formed by two dies to cast a casting part. The common metal is aluminum or aluminum alloys. The pressure is usually 10–140 megapascals. That’s why it’s sometimes called high-pressure die casting. This process shares similarities with the plastic manufacturing process of injection molding. It is one of the most popular process of metal casting. Due to its high accuracy, good quality, and ability to create detailed components.
Usually, non-ferrous metal alloys with a low melting point are raw materials. Such as zinc, copper, aluminum, magnesium, lead, tin, tin-based alloys. According to the type of metal being cast, there are Hot Chamber Die Casting Method and Cold Chamber Die Casting Method
Die Casting Types
Hot Chamber Die Casting Method
Hot Chamber Die Casting – Best for low-melting-point metals like zinc. The injection mechanism is submerged in molten metal.
This process is used for low-melting alloys. Such as zinc, lead, tin, magnesium alloys. One feature of hot chamber die casting machines is that the casting chamber is constantly in contact with the liquid alloy. The melt passes through a valve into the casting chamber. At there, it is pressed at high speed into the closed die casting mold by the piston. Hot-chamber die casting is a great option for alloys that do not readily attack and erode metal pots, cylinders, and plungers.
Cold Chamber Die Casting Method
Cold Chamber Die Casting – Used for high-melting-point metals like aluminum. The molten metal is ladled into the chamber for each shot.
This process is better suited for metals with high melting points such as aluminum, copper.In the cold chamber die casting process, metal is liquefied. Then ladled into a cold chamber. At there, a hydraulically operated plunger pushes the metal into the mold. After the alloy has been pressed into the mold in both processes, the component solidifies under strong pressure. Then remove from the mold. t can be further processed if necessary.
Die casting Applications
Die casting is used in industries such as:
– Automotive (engine parts, transmission housings)
– Aerospace (lightweight components)
– Electronics (heat sinks, connectors)
– Consumer goods (appliance parts, power tools)
– Medical devices (precision instruments)
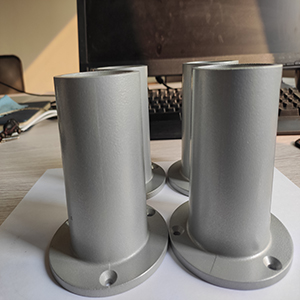
Advantages and Disadvantaged of Die Casting
Advantages:
– High production rate
– Tight tolerances (±0.002 in.)
– Smooth surfaces (can eliminate machining)
– Thin-walled parts possible
– Good strength-to-weight ratio
Disadvantages:
– High initial die cost (justified for large production runs)
– Not economical for small batches
– Limited to non-ferrous metals (typically)
How are Die Castings Made?
To produce tens of thousands of castings at high speed, the steel mold must be made in at least two sections to allow the castings to be removed. These parts are firmly mounted in the machine and are arranged so that one is stationary (fixed die half). The other one is movable (syringe half-mold). To begin the casting cycle, the two mold halves are clamped together by a die-casting machine. Molten metal is injected into the mold cavity and rapidly solidified. The mold half is opened and the casting is ejected. Die-casting molds can be simple or complicated, with moveable slides, cores, or other parts. This is depending on the complexity of the casting.
Until now, the die casting cycle has been the fastest cycle to produce precision nonferrous metal parts. This is in stark contrast to sand casting. It requires new sand molds for each casting. Although the permanent mold process uses iron or steel molds instead of sand. It is much slower and less precise than die castings.
Die Cast Process
Die Casting Material Types
Material | Tensile Strength (Mpa) | Thermal Conductivity (W/mK) | Features |
---|---|---|---|
Aluminum A380 | 325 | 96 | Best combination of mechanical, casting, and the thermal properties.Excellent fluidity, pressure tightness, and resistance to hot cracking.Widely used for engine brackets, hand tools, electronic equipment chassis, gearbox cases, and household furniture. |
Aluminum A360 | 317 | 113 | Excellent pressure tightness and fluidity.High corrosion resistance.High strength in elevated temperatures. |
Aluminum 413 | 295 | 121 | Good combination of casting, mechanical, and thermal properties.Excellent fluidity, pressure tightness, and resistance to hot cracking. |
Aluminum 383 | 310 | 96 | Often used for highly intricate components.Good corrosion resistance, lightweight. Good combination of casting, mechanical, and dimension stability. |
Aluminum B390 | 317 | 134 | High hardness and good wear resistance.Suitable for internal combustion engine pistons, cylinder bodies for compressors, and brakes. |
Aluminum A413 | 290 | 121 | Excellent pressure tightness.Good choice for hydraulic cylinders. Suitable for die casting intricate components. |
ZAMAK 2 | 359 | 105 | Excellent damping capacity and vibration attenuation.Superior to other Zamak alloys with creep performance.High strength and hardness levels after long-term aging |
ZAMAK 3 | 283 | 113 | Great balance of physical and mechanical properties.Excellent finishing characteristics for plating, painting, and chromate treatments.Good castability and long-term dimensional stability.Good damping capacity and vibration attenuation. |
ZAMAK 5 | 328 | 109 | Has a higher copper content than Zamak 3, which results in higher strength.Has less ductility than Zamak 3. More readily plated, finished, and machined than Zamak 3. |
ZA 8 | 374 | 115 | Ideal for decorative application.Excellent finishing and plating characteristics.Good performance of strength, hardness, and creep properties. |
Secondary Operations of Die Casting
- High precision CNC machining, milling, drilling, tapping, e-coating, anodizing
- Painting, sanding, shot blasting, powder coating, chrome plating
Typical Die Casting Parts
AL Mg,Zn