1. Bubbles
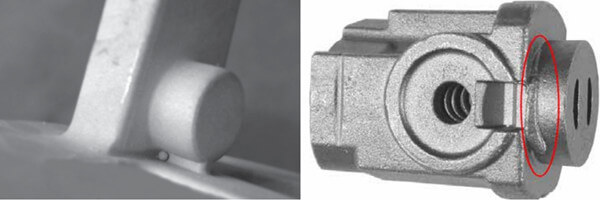
Mechanism
Air trapped against the wax pattern by the primary slurry layer
Description
- Defect Type: Positive
- Appearance: Small, smooth spherical, oval or elongated tubular shaped positive。
- Size:1/8” or less
- Typical Location: Difficult to wet out areas during shell building
- Similar to: Wax bubbles (see Atlas of Wax Pattern Defects)
- Aliases: BBs, Air Bubble
- Method for defect determination: Visible to eye. Smooth surface of the defect
Area | Possible Cause | Potential Correction |
Wax | Bad mold design | Re-orient the part to prevent air from being trapped during dipping |
Shell | Poor dipping technique | Immerse the pattern slowly in the slurry, use vibration or, compressed air or vacuum to pop any trapped air bubbles |
Shell | Poor draining technique | Back drain slurry into areas that cannot be wet out during dipping |
Shell | Incomplete pattern wetting | Use a pre-wet or use a lower prime coat viscosity |
Shell | Insufficient slurry wetting | Ensure the correct amount of wetting agent is in the slurry |
Shell | Incomplete pattern cleaning | Ensure the silicone is removed from all surfaces of the pat terns and no air bubbles are preventing proper cleaning |
Shell | High air level in the slurry | Ensure air is not being sucked into the slurry by the mixer. Conduct antifoam test and adjust if necessary |
2. Buckle

Mechanism
The bond strength of the primary layer to the wax patter is insufficient and the primary layer buckles (lifts) off the pattern. The bond strength can be insufficient for a number of reasons including stress on the primary layer as it shrinks during drying.
Description
Defect Type :Positive
- Appearance: Faceted or pyramid-like surface with a distinct ridgeline often associated with flash
- Typical Location: Flat featureless surfaces
- Similar to: Prime coat lift
- Method for defect determination: When a shell buckles, it only separates from the pattern.
With prime coat lift, the shell also fractures, allowing the backup layers to fill the gap between the primary layer and the wax pattern.
Area | Possible Cause | Potential Correction |
Wax | Temperature change in wax causes the wax to move and disrupt the primary layer bond. Wax pat tern temperature not stable | Ensure the wax pattern has stabilized in temperature before applying shell layers |
Wax | Pattern cleaning inadequate. Poor adhesion of the primary coat to the wax pattern | Increase etch strength or, time in etch. Reduce the time from etch to primary layer |
Wax | Pattern flexing during dipping | Add additional pattern supports |
Shell | Large temperature change | Control the dipping area to +/- 3 F |
Shell | Drying too long | Set a maximum dry time |
Shell | Drying too short | Insure the primary layer is completely dry before applying backup layers |
Shell | Poor prime coat wetting | Confirm the prime slurry is wetting the pattern |
Shell | Low adhesion binder | Increase polymer level |
Shell | Drying too fast (high pattern shrinkage & drying stress) | Slow down (Increase) the drying by reducing airflow or increasing room humidity or reduce airflow |
Shell | Pre-wet is lifting prime | Eliminate pre-wet or reduce dry time between pre-wet and slurry application |
Shell | Too much slurry on interior surfaces | Decrease slurry viscosity or increase drain time |
Shell | Too little slurry on interior surfaces | Increase slurry viscosity or decrease drain time |
Shell | Insufficient stucco on interior surfaces | Don’t let slurry surface dry or over drain before stucco application |
Shell | Primary slurry in poor condition | Employ proper slurry controls |
Shell | Soaking (saturating) the mold promotes lifting. Vibration too high | Vibration used during dipping can cause the primary coat to separate from the pattern |
Shell | Pattern flexing during dipping | Add additional pattern supports |
Shell | Soaking (saturating) the mold promotes lifting. Vibration too high | Stucco molds immediately after slurry have drained |
Shell | Thermal expansion mismatches within the shell | Change shell composition |
Shell | Pattern is too flat and featureless | Add ribs or dimples to break up flatness and create features |
Other (Mold design) | Pattern flexing during dipping | Add additional pattern supports |
3. Bulge
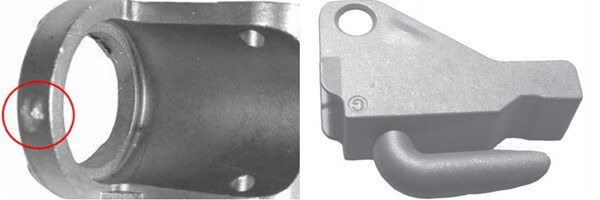
Mechanism:
The permanent defection of the mold wall either during dewaxing or casting.
Description
- Defect Type:Positive
- Appearance:Gradual thickening of the casting wall. May have finning in the area of the bulge. May not be detectable by the naked eye but can be caught by gauging.
- Typical Location:Parallel surfaces, deep holes, or slots. Adjacent patterns on assembly. Large flat featureless surfaces
- Similar to:Similar in appearance to shell buckle but it doesn’t have the definitive shape of a crack in the casting.
- Aliases:Bulging, bulging cracking, bulging overheating, shell bulge
- Method for defect determination: Shell bulge generally has a more rounded surface
Area | Possible Cause | Potential Correction |
Wax | Patterns too close cause premature bridging | Use spacers during assembly to produce consistent pattern spacing |
Shell | Shell too thin | Add shell layers or add stiff ening feature |
Shell | Mold hot strength too low (mold creeping during casting cooling) | 1) Increase refractoriness of the shell2) Ensure optimal SiO2 levels in the backup slurry3) Ensure uniform mold thickness |
Shell | Slurry not wetting out area | 1) Use vacuum dipping or re-orient pattern.2) Use a thinner slurry |
Shell | Slurry/stucco not getting into area | Use a “poured core” |
Shell | Stucco not getting into the area | 1) Rainfall, hand pour or re-orient pattern2) If bridging in slots or holes, use a finer stucco or make sure hole is open prior to applying subsequent dips until sufficient slurry/stucco has been applied |
Shell | The slurry is being washed away when subsequent coats are applied | Ensure sufficient intra-coat dry time and conditions for hard to dry areas of the mold |
Shell | The green strength of the shell is too low to withstand dewaxing | 1) Increase the dry time between each layer2) Apply additional coats3) Increase final dry time4) Redesign assembly to permit a more rapid heat transfer to all parts of mold5) Vent pattern cavities6) Check dewax process for optimal performance and that it is in control |
Shell | Deformation during dewaxing | See “Finning” |
Foundry | Solidification time too long | Decrease metal temperature, decrease mold temperature, speed casting cooling rate |
Foundry | Ferrostatic pressure too high | Reduce vacuum level, reduce spinning rate (centrifugal) |
Foundry | Ferrostatic pressure too high | Reduce the metal height above the part |
4. Cold Shut
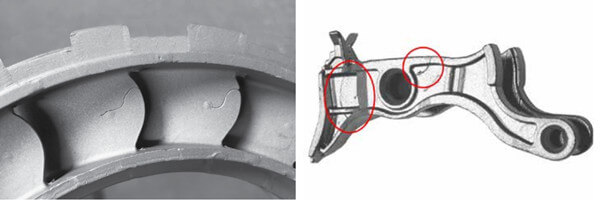
Mechanism
The incomplete joining of two metal fronts
Description
- Defect Type:Negative
- Appearance:Smooth, linear, shallow, rounded edged impression extending into feature wall. This defect takes the form of a crack or discontinuity in the surface with rounded edges indicating the freezing or solidification of two or more streams of metal before they had time to completely fuse together.
- Size:varies
- Typical Location: Thin sections or areas furthest away from gate where two metal
- fronts meet.
- Similar to: Wax knit line (see Atlas of Wax Pattern Defects)
- Aliases: Cold Shot, Short Fill
- Method for defect determination:Penetrant inspection, visual inspection, metallographic inspection for evidence of non-bonding along line below cast surface. A wax knit line will have not extend below cast surface ceramic in the junction.
Area | Possible Cause | Potential Correction |
Foundry | Metal not hot enough | Increase metal superheat |
Foundry | Mold not hot enough | Increase mold temperature/ increase or add mold insulation |
Foundry | For air cast, mold not permeable resultingin backpressure/trap ping air that slows | Reduce shell thickness or gating design to fill pattern cavity from more locations.Add vents. Increase shell permability |
Foundry | metal fill time | Consider modifications to alloy composition |
Foundry | Poor metal fluidity | Increase pour rate |
Foundry | Slow metal pour rate | Maintain a steady pour rate until mold is full |
5. Core Breakage
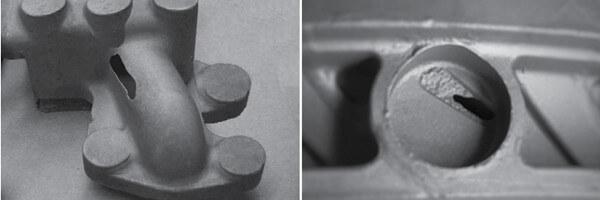
Mechanism
Core breaks either during wax injection, during mold heating, or during metal pouring
Description
- Defect Type: Negative
- Appearance: Metal fin across an area that is formed by a ceramic core. In the case of core break and shift, missing metal where a wall should be.
- Size: varies
- Typical Location: Can only occur on casting made with ceramic core
- Method for defect determination: Visual, X-ray in case of hidden from view.
Area | Possible Cause | Potential Correction |
Wax | Mold design creates stress on core upon clamping or wax injection | Examine the need for core print relief or core supports to reduce stress |
Shell | Poor core slipping method | Examine for too many core locks or “prints” |
Other (Mold design) | Too high of wax injection pressure | Reduce injection pressure |
6. Crack
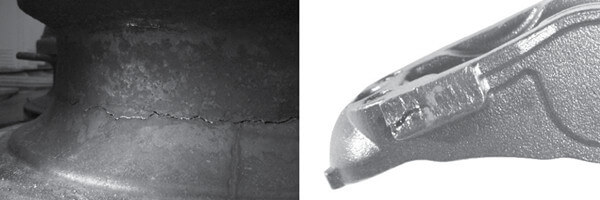
Mechanism
Typically, internal stresses from solid-state cooling or rapid cooling can cause cracking.
Description
- Defect Type: Negative
- Appearance: Jagged crack with irregular path
- Typical Location: Geometry involves seriously restrained contraction or in a local volume of unfed metal. May occur at the intersection of the thick and thin section.
- Similar to: Hot Tear
- Method for defect determination: Visual inspection and Penetrant inspection typically reveal cracks. Cracks form roughly 90° to stress direction.
Area | Possible Cause | Potential Correction |
Wax | Restriction of casting contraction at elevated temperature | Modify gating to prevent strong gates or runners from preventing the casting from contracting |
Wax | Premature movement of mold after casting | Modify the design to avoid contraction restriction and strengthen the weak areas by the use of webs |
Foundry | Uneven cooling rate-The use of water to cool a hot casting can set up high internal stress | Allow time for the casting to solidify before moving |
Other (Post-cast operation) | Removal of cast material can create an imbalance of the internal stress leading to cracking. | Avoid rapid cooling methods |
Other (Post-cast machining) | Restriction of casting contraction at elevatedtemperature | Add a stress-relief thermal cycle to as-cast part prior to metal removal operations |
Other (Casting design) | Major sectional changes in the casting design | Modify the design to avoid contraction restriction and strengthen the weak areas by the use of webs |
Other (Casting design) | Sharp internal angles | Modify gating to prevent strong gates or runners from preventing the casting from contracting |
Other (Casting design) | Restriction of casting contraction at elevated temperature | Ensure adequate fillet radii |
7. Cut-off Damage
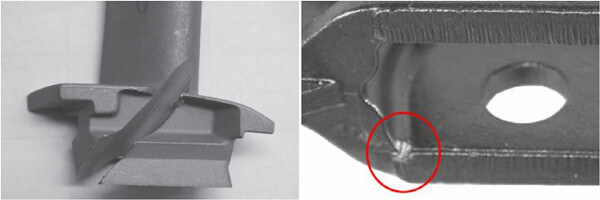
Mechanism
Blade or plasma torch deflects into casting or continues into casting after cut.
Description
- Defect Type: Negative
- Appearance: Slot or beveled face with characteristic grooves running the direction of the cut-off wheel
- Typical Location: Anywhere but typically near a gate contact
- Method for defect determination: Visual inspection
Area | Possible Cause | Potential Correction |
Other (Gating Design) | Castings too close to the runner bar/ variable distance from runner bar | Increase gate length |
Other (Post-Cast operation) | Incorrect part loading in cutoff fixture | Mistake proof the holding fixture |
Other (Post-Cast operation) | Cut-off blade flex during the cut-off | Use different blade, change gate shape |
8. Delamination
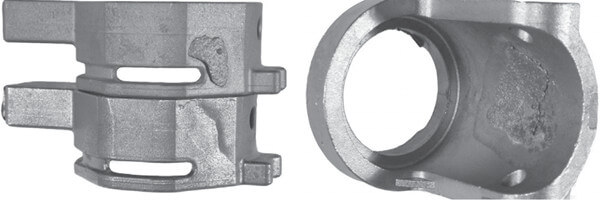
Mechanism
Failure of bond between 1st and 2nd layer of shell. The first layer is pushed or pulled into
the mold cavity usually during dewax. Sometimes the shell cracks and metal fills the gap between the layers producing a scab.
Description
- Defect Type: Negative
- Appearance: Faceted metal indentation sometimes accompanied by a positive metal scab
- Typical Location: Flat featureless surfaces
- Aliases: Scabbing, Reverse Buckle
- Method for defect determination: Visual, appears as scab with indentation under a scab.
Area | Possible Cause | Potential Correction |
Shell | Incomplete wetting between 1st and 2nd layer | Blow off loose primary coat stucco. Ensure immersion time in 2nd layer slurry is adequate to wet-out the primary layer |
Shell | Etch too strong – too tacky | Reduce etch strength or time |
Shell | Drying rate of 2nd layer is too high | Increase drying room humidity |
Shell | Poor bond between prime and backup layer | Ensure adequate keying between the primary and first backup coat. Use a coarser or more angular primary coat stucco to blow off loose or excess stucco |
Shell | Moisture trapped be hind the primary coat | Ensure adequate drying of the mold prior to dewaxing |
Shell | Differential expansion stresses between the primary and secondary coats | Ensure the thermal expansion of the primary coat is compatible with that of the shell coats |
Shell | Rapid pressure release during autoclave dewaxing | Autoclave blowdown should be gradual and take 2 minutes or more |
9. Distortion
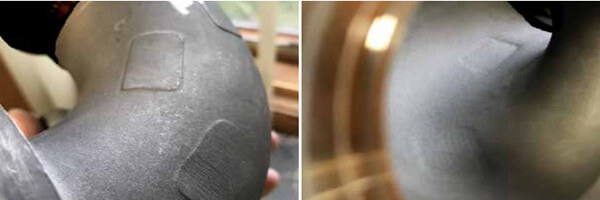
Mechanism
Distortion of the casting occurring at wax injection, pattern assembly, or casting cooling.
Description
- Defect Type: Shape.
- Appearance: The geometry does not conform to the drawing.
- Size: varies.
- Typical Location: Opposite gate locations.
- Similar to :Sink, Cavitation (See Atlas of Wax Pattern Defects).
- Method for defect determination: Visual inspections and customary dimensional inspection tools.
Area | Possible Cause | Potential Correction |
Other (Casting design) | Geometry of the casting and or running system causing uneven contraction | Minimize uneven stresses that develop with solid-state metal contraction occurs |
Other (Mold design) | Improper gating system design | Design the gating and runner system to prevent uneven stresses |
Other (Mold design) | Ingates contracting and pulling part of the casting | Examine the runner system and modify to reduce stresses |
Wax | Improper wax pattern handling ejected from die | Modify release agent spraying technique, frequency. Add ejector pins |
Wax | Improper wax pattern storage | Store patterns in a manner to prevent distortion |
Wax | Ingates contracting and pulling part of the casting | Examine the runner system and modify to reduce stresses |
Wax | Improper gating system design | Design the gating and runner system to prevent distortion |
Shell | High strength mold preventing even contraction | Reduce the mold strength |
Other | Knockout conducted at too high a temperature | Knockout at a lower temperature |
Foundry | Improper casting handling | Ensure cast molds are handled with care – especially at high temperature |
Other (Heat treatment) | Stresses induced during heat treatment | Ensure the castings are correctly supported during heat treatment. Use the slowest quenching method that will achieve the required hardness |
10. Etch Spotting
Mechanism
During pattern cleaning prior to shell building, the etch solution is not completely rinsed off. The etch continues to attack the wax forming rings or drips on the bottom of the pattern.
Description
- Defect Type: Negative and Positive
- Appearance:Smooth. Raised droplet or “coffee ring” like appearance where ring may be slightly indented into casting
- Special Circumstances:Most common with difficult to rinse etch solutions
- Size: ¼” or less
- Typical Location: End of part away from the pour cup. Areas where etch rinse water beads up after pattern cleaning or there is insufficient rinse action on the surface of wax. Often in deep corners but can occur on open surfaces.
- Aliases: Fisheyes
- Method for defect determination: Monitor the etching operation and inspect wax patterns prior to first dip in pre-wet or primary dip
Area | Possible Cause | Potential Correction |
Shell | Incomplete rinse after pattern etch | Increase agitation during rinse, keep rinse water clean and/or use multiple rinse tanks. Last rinse water should always be clear to ensure cleanliness. Make sure water temperature is room temperature. |
Shell | Incorrect etch concentration | Some etch products require mixing with water prior to use. Verify measurements and test concentration if possible. |
11. Excess Metal
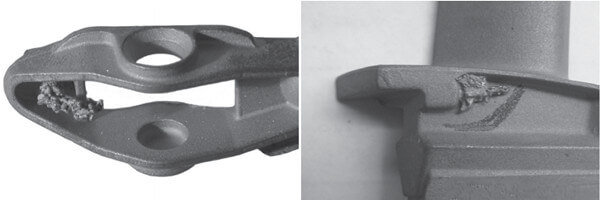
Mechanism
Thin or weak areas of the shell fail during dewax or casting allowing metal to leak into the void in the shell.
Description
- Defect Type: Positive
- Appearance: Irregular shaped mass typically attached to the casting by flash
- Size: Varies but typically metal is restrained by external shell geometry
- Typical Location: Holes, slots, or tight corners
- Aliases: Metal breakthrough, Metal Penetration, Core Collapse
- Method for defect determination: Visual Inspection.
Area | Possible Cause | Potential Correction |
Other (Mold design) | Poor mold design | Re-orient the part to improve slurry and stucco coverage |
Shell | Poor shell build/slurry / stucco schedule | Improve wetting of detail by shell code changes, reorienting the part or vacuum dip ping, thinner slurries and finer stuccos, use intermediate slurry and or stucco |
Shell | Incomplete loose stucco removal | Blow loose stucco out of detail, slots or blind holes |
Shell | Incomplete slurry wetting | Change pattern orientation,use vacuum dipping, lower the slurry viscosity or use prewet solutions |
Shell | Incomplete drying | Increase the dry timebetween layers |
Shell | Incomplete stucco coverage | Pour stucco into the area, change orientation of the pat tern, use finer or intermediate stucco |
Shell | Stucco too large | Change shell code, use finer stucco |
Shell | Stucco contains large particles (“rice krispies” or “snerds”) | Sift the large particles out of the stucco |
Shell | Dewax cracking | Improve dewax performance |
Shell | Autoclave depressurization too rapid | Gradually depressurize the autoclave over 2 minutesor more |
Other (Casting design) | The core length to cross-sectional area too great to allow production of a sound core by normal shell techniques | Form area with “poured core” or preformed ceramic core |
12. Finning
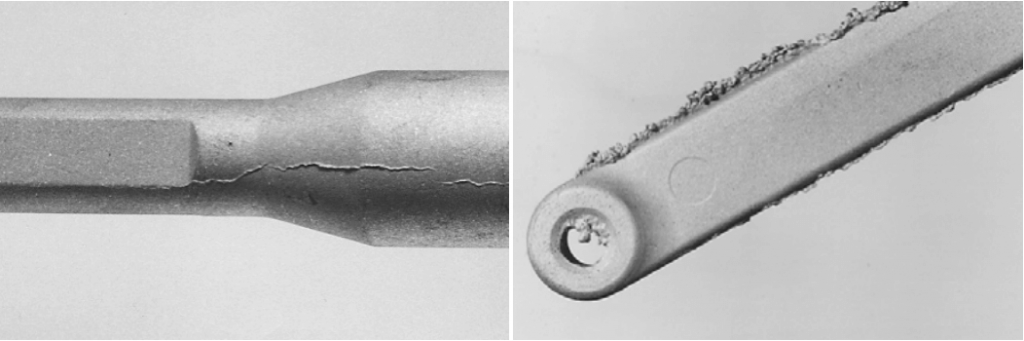
Mechanism
Shell crack during shell building, drying or dewaxing, and molten metal fills the crack during casting. Cylindrical shapes are more prone to this defect due to hoop stress
Description
- Defect Type: Positive
- Appearance:Sharp, linear fin of metal perpendicular to the surface
- Typical Location: Flat featureless surfaces, sharp edges or cylindrical parts, across holes
- Similar to: Wax flash (See Atlas of Wax Pattern Defects)
- Aliases: Flash, Shell Crack, Mold Crack
- Method for defect determination: Wax flash can only be located on the parting line of the pattern.
Area | Possible Cause | Potential Correction |
Wax | Runner wax melts too slow creating increased pressure by part wax on mold as it melts | Change the formulation of the runner wax to insure it melts as fast or faster than the pattern wax, use a low melting point wax to apply “dip seal” to the runner system |
Wax | Pattern wax does not bleed through the mold during dewaxing | Change pattern wax or increase green permeability |
Wax | Wax flash/parting line not removed | Removal of all parting line indications |
Shell | Low mold strength | Add an additional shell layer, use a polymer, and increase SiO2 of slurry |
Shell | Incomplete mold drying | Increase the mold dry time |
Shell | Slow autoclave pressurization | The autoclave should rapidly pressurize to 80 psi in 10 seconds or less |
Shell | Large temperature fluctuations during drying | Maintain 3F maximum temperature variation |
Shell | Inadequate dewax pressure relief | Add venting to difficult to dewax areas |
Shell | Slow dewax loading | Load dewax unit quickly to reduce mold exposure to heat |
Shell | Pattern wax does not bleed through the mold during dewaxing | Change pattern wax or increase the shell permeability |
13. Gas
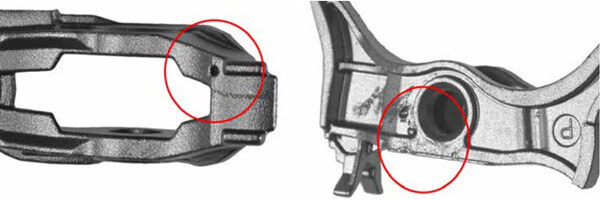
Mechanism
During casting, turbulent flow mixes the air that is exiting the mold with the metal that is entering. These bubbles float to the surface of the metal but are trapped by the solidifying metal. (Like air bubbles trapped under a layer of ice). This also can be caused by incomplete burnout of the wax and filler material in the mold, igniting when the molten metal reaches this material.
Gasdefects can also be formed when ceramic cores out-gas, or the strengthening materials (such as binders or superglue) applied to cores, burns out (usually associated with low preheat temperatures). Low permeability of molds is another cause of entrapped gas.
Description
- Defect Type: Negative
- Appearance: Round smooth walled cavities may exhibit a slightly oxidized surface of varying diameter.
- Size: 0.5 to 4 mm
- Typical Location: Generally located in the upper region of the part as-cast
- Similar to: Pinholes, Blowholes, Slag, Incomplete Burn-out.
- Aliases: Entrapped Air, Porosity
- Method for defect determination:Upper region of the part as-cast, only a few holes. Fewer number of cavities than pinholes
Area | Possible Cause | Potential Correction |
Other (Mold design) | Poor gating design | Add vent at top of part to allow air to escape |
Other (Mold design) | Poor gating design | Modify gating system to prevent turbulence during metal filling |
Other (Mold design) | Low ferrostatic pressure | Increase the height of the mold, use vacuum assistance, centrifuge |
Shell | Low mold permeability | Increase the mold permeability or use vacuum assistance during the pouring |
Foundry | Bad pouring practice | Reduce height from ladle to mold, pour down the side of the pour cup |
Foundry | Excessively turbulent metal flow into the mold. Low ferrostatic pressure | Modify the gating technique to give less turbulent flow; self-venting mold. Increase the height of the mold, use vacuum assistance, centrifuge |
Foundry | Low metal temperature | Increasing the metal temperature allows more time for gas bubbles to escape before skin is formed |
Foundry | Excess wax and filler material after dewaxing mold | Burn molds out fully prior to preheating. Add excess oxygen to preheat/ burnout oven to ensure complete burnout of mold. |
Foundry | Poor deoxidation practices | Improve practices |
Foundry | Moisture contained within the metal feedstock | Ensure metal is free from moisture rust or lubricants. |
14. Grinding Damage
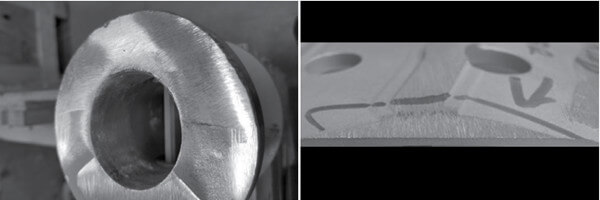
Mechanism
Abrasive grinding belt or wheel continues grinding into casting after removing the gate
Description
- Defect Type: Negative
- Appearance: Missing features or low wall thickness with linear serrations
- Typical Location: Near gates or on same surface as gates
- Similar to: Cutoff Damage.
Area | Possible Cause | Potential Correction |
Other | Grind depth set too deep | Ensure grinding depth set correctly on automatic grinder |
Other | Part improperly loaded | Mistake proof part loading on the grind fixture |
Other | Residual ceramic prevents proper fixture loading | Improve ceramic removal method |
Other | Incorrect belt width | The contact wheel and grinding belt should be sized according to the gate width |
Other | Snagging from loose grip in operator’s hand | Hold casting tight in hand when approaching belt or disc |
Other | Excess Snagging from inability to see grind area interface | Change view angle |
Other | Incorrect grit size on belt | Ensure belt grit size before grinding |
15. Handling Damage
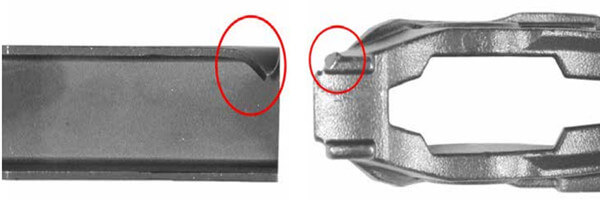
Mechanism
Castings are damaged at some point after solidification
Description
- Defect Type: Negative and positive
- Appearance: Dinged surface. Smooth negative with accompanying positive burr, dented edge, rolled corner, bent or distorted metal
- Size: Various
- Typical Location: Protruding features, corners, thin areas
- Similar to:Wax damage (See Atlas of Wax Pattern Defects)
- Aliases: Knockout Damage
- Method for defect determination: Visual or dimensional gauging.
Area | Possible Cause | Potential Correction |
Foundry | Damage occurring during handling | Prevent operators from dropping castings onto one another |
Other (Knockout/cutoff/blasting) | Damage occurring during mechanical cleaning | Reduce tumbling speed or add cushioning material with castings (addition of rubber blocks during tumble blast) |
Other(Transporting) | Damage occurring during transportation | Ensure floors are level, wheels on carts are adequate |
16. Hot Tear
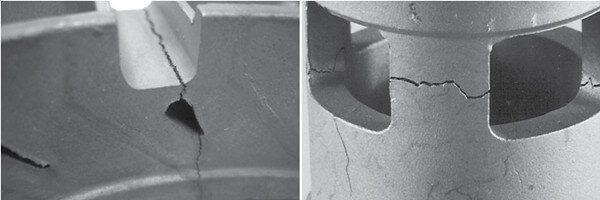
Mechanism
During casting cooling, the strength of the shell or gating system exceeds that of the solidifying metal.
Description
- Defect Type: Negative
- Appearance: Jagged crack with irregular path, typically with an oxidized fracture face
- Typical Location: Slow to cool or solidify areas where the geometry involves seriously restrained contraction or in a local volume of unfed metal. May occur at the intersection of thick and thin section.
- Similar to: Crack, Wax Crack (See Atlas of Wax Pattern Defects)
- Aliases: Shrinkage Crack
- Method for defect determination: A wax crack will typically contain refractory and have a somewhat smooth, non-dendritic fracture face.
Area | Possible Cause | Potential Correction |
Wax | Restriction of casting contraction at elevated temperature | Modify the design to avoid contraction restriction and strengthen the weak areas by the use of webs. |
Wax | Major sectional changes in the casting design | Modify gating to prevent strong gates or runners from preventing the casting from contracting |
Shell | Sharp internal angles | Ensure adequate fillet radii |
Shell | Gating incorrect | Reduce mold strength. |
Shell | Shell too strong | Modify gating to prevent strong gates or runners from preventing the casting from contracting Use a slower cooling rate |
Foundry | Premature movement of mold after casting | Reduce shell layers. Allow time for the casting to solidify before moving |
Foundry | Uneven cooling rate | Allow time for the casting to solidify before moving |
Foundry | Gating incorrect | Sink mold after casting or wrap in insulation |
Foundry | Metal chemistry | Reduce mold strength. |
Foundry | Metal chemistry | Modify gating to prevent strong gates or runners from preventing the casting from contracting Use a slower cooling rate |
Other (Mold design) | Gating incorrect | Use certified virgin ingots |
Other (Casting design) | Sharp internal angles | Modify the metal chemistry |
Other (Casting design) | Casting design | Reduce mold strength. |
Other (Mold design) | Restriction of casting contraction atelevated temperature | Modify gating to prevent strong gates or runners from preventing the casting from contracting Use a slower cooling rate |
Other (Casting design) | Major sectional changes in the casting design | Ensure adequate fillet radii |
17. Incomplete Burn-out
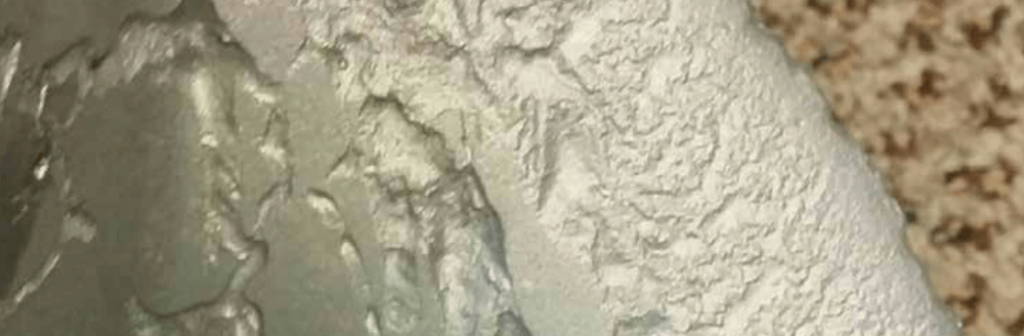
Mechanism
During casting, residual carbon in the mold remaining from incomplete burnout reacts with molten metal producing CO. The CO, in the form of a gas bubble, prevents the metal from filling the area
Description
- Defect Type: Negative
- Appearance: Smooth irregular shaped voids generally in or just under the cast surface usually irregular in outline but tending to assume a spherical or wormlike shape. The casting surface may exhibit a matte finish in the area of the defect
- Size: 1 to 4 mm
- Typical Location: Sections of mold that don’t drain during dewaxing. Areas of mold that are densely packed when shell built.
- Similar to: Gas, Slag
- Alias: Ash
- Method for defect determination: Gas tends to be on the upper surface or the part during casting. Metal mold reaction is located where the carbon does not burn out.
Area | Possible Cause | Potential Correction |
Other (Mold design) | Poor wax drainage | Orient the parts to allow for a high level of wax drainage from the mold |
Other (Mold design) | Patterns too close | Increase spacing between patterns to prevent shell bridging |
Wax | Patterns too close | Increase spacing betweenpatterns to prevent shell bridging |
Wax | High ask content in wax | Use a low ash content wax |
Shell | Incomplete wax removal | Insure the dewax cycle time is adequate to remove all of the wax |
Foundry | Short mold burn-out time | Increase burnout time |
Foundry | Insufficient air circulation in the mold | Place molds on stand or ribbed hearth plate |
Foundry | Low oxygen level in the burnout furnace | Increase excess air |
Foundry | Contamination of the mold | Rinse mold and/or cover pour cup to prevent contamination |
18. Leaker
Mechanism
Metal leaks out of the mold during or immediately after casting
Description
- Defect Type: Negative
- Appearance: Smooth in most instances, but also be rough. It could be irregular. Many features or runners missing because of lack of metal. May have a positive fin where the leaker occurred.
- Typical Location: Top of casting as oriented during casting
- Aliases: Runout, Short Pour
- Method for defect determination: Visual inspection.
Area | Possible Cause | Potential Correction |
Wax | Handling damage | Examine process and add preventive measures |
Shell | Broken shell handling damage. | Improve dewaxing perfor mance or dip molds after dewaxing, mold handling to prevent damage to the mold |
Shell | Low mold strength | Verify slurry in spec and control or add shell layers |
Shell | Dewax cracking | Fill mold with colored dye/water mix to identify crack locations. Add wax vents.Improve dewaxing performance |
Shell | Poor patch coverage–incomplete drying | Modify patching procedure to insure complete drying prior to placing in burnout oven |
Shell | Handling damage | Examine process and add preventive measures |
Foundry | Rough handling of hot mold | Examine process and add preventive measures |
Foundry | Handling damage | Examine process and add preventive measures |
19. Non Fill
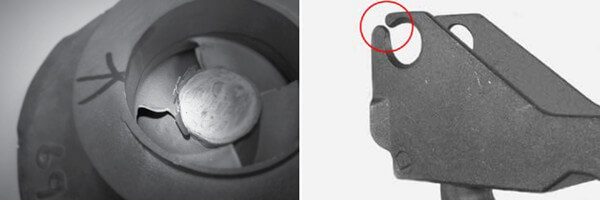
Mechanism
During casting, the metal freezes before mold cavity is completely filled out
Description
- Defect Type: Negative
- Appearance: Incomplete casting with rounded edges where casting is not completely formed
- Typical Location: Thin sections and sharp edges away from the gate
- Similar to: Cold Shut, Wax non fill (See Atlas of Wax Pattern Defects)
- Aliases: Misrun
- Method for defect determination: Visual Inspection.
Area | Possible Cause | Potential Correction |
Shell | Low mold permeability | Increase shell permability. Consider reducing shell thickness. Vent thin sections |
Foundry | Low metal pouring temperature | Increase metal temperature, improve ladle preheating, speed time from tap to pour |
Foundry | Low mold temperature | Speed time from oven to cast or insulate mold to prevent heat loss |
Foundry | Interrupted pour. | Pour without interruption |
Foundry | Lack of metal fluidity | Increase fluidity by reducing metal oxides or adjustment of the metal chemistry |
Foundry | Poor gating system | Modify gating design to create more entry points for alloy |
20. Non-Metallic Inclusion
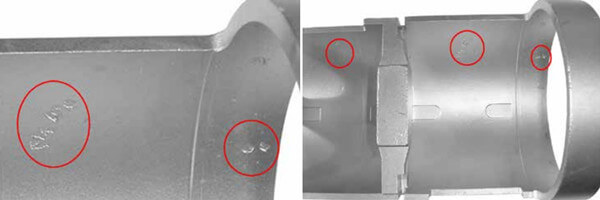
Mechanism
Foreign material in the mold cavity which can originate either from the mold or from outside the mold. The shape of the defect aids in determination of the source
Description
- Defect Type:Negative
- Appearance: Generally a smooth sided irregular negative shape of indefinite size. Inclusions caused by ceramic material are usually more angular and may contain bits of embedded ceramic.
- Size: Variable
- Typical Location:Most obvious on external surface of casting where the “inclusion” prevented the alloy from filling the mold cavity to the shell surface.
- Aliases:Dirt, Ash
- Method for defect determination:Visual Inspection.
Area | Possible Cause | Potential Correction |
Wax | Junction between wax gate and sprue not completely sealed (undercuts). Ceramic fills the undercut during shelling and breaks off during dewax or pouring. | Improve gating technique to eliminate undercuts. Make sure wax joints (parts to sprue) are sooth and complete. |
Wax | Filter breakage | / |
Wax | Ash in wax – as in wax typically floats in the molten alloy and is present on the top side of castings | Test ash content of wax |
Wax | Incomplete soluble removal | Confirm soluble leaching process and inspection is adequate |
Wax | Filler settles out in areas that do not drain during dewaxing | Reconfigure gating design to improve wax removal. Add wax bleeder |
Shell | Cracks in mold and ceramic bits get into mold cavity | See Finning |
Shell | Poor mold patching technique – patch enters mold | Improve patch technique |
Shell | Poor adhesion of shell layers to one another | See Spall |
Shell | Ceramic debris entering mold after dewaxing(poor housekeeping) | Cover the pour cup after dewaxing (allow moisturefrom the mold to escape).Store the mold cup down. Wipe rim of pour cup beforeturning up-right |
Shell | Ceramic breaking loose inside the mold during dewaxing | Vacuum or wash out mold after dewaxing |
Shell | Slurry floods pour cup during shell building | Cover pour cup, immediately rinse slurry out. Remove alldried ceramic prior to dewaxing. Coat the inside of the pour cup with wax prior to shelling to aid in slurry removal from cup during dewax. |
Shell | Ceramic material from jagged lip/edges on in house shell built pouring cups is broken off during handling, burnout or casting | Use a preformed ceramic pour cup or assure in house shelled cup is uniform and robust on top edge |
21. Overblast
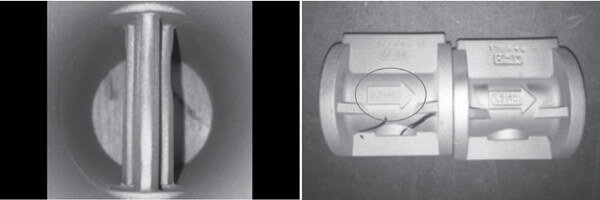
Mechanism
The blasting media used in mechanical cleaning equipment is typically harder than the casting. The surface of the casting can be deformed or eroded by extended blasting time or excessive blasting energy.
Description
- Defect Type: Negative
- Appearance: Small negatives possibly with accompanying burrs. Textured surface. May have rolled edges. Eroded features
- Typical Location: Surfaces exposed to shot or sand blast media.
- Aliases:Blasting damage
Area | Possible Cause | Potential Correction |
Other | The casting are too hot during blasting | Allow parts to cool prior to blasting |
Other | Castings are stopped in front of the blasting nozzle or wheel | Insure the parts are constantly moving during the blasting cycle. Check the mill or spinners to confirm movement duringthe blast cycle |
Other | Blast time is too long | Reduce blast time |
Other | Blast media is too large | Reduce blast media size |
Other | Blast media is too hard | Use softer blast media |
22. Oxide
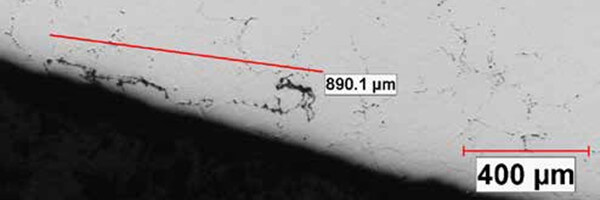
Mechanism
During casting a refractory oxide skin is formed in the melt through the exposure of reactive elements to oxygen. Certain elements are more reactive than others and will preferentially oxidize. The metallic oxide that is formed can be aggravated with turbulent filling.
Description
- Defect Type: Negative
- Appearance: Metallic oxides are thin black sub-surface streamers forming an irregular pattern or agglomeration on the surface of the casting.
- Special Circumstances: More commonly encountered with alloys containing highly reactive elements (Ti, Al, Zr, Cr, etc.)
- Size: Varies
- Typical Location:Surface and subsurface
- Similar to: Rat-tailing, Cold shut, Slag
- Aliases: Oxide Folds, Dross, Slag, Oxide Film
- Method for defect determination: Metallic oxide indications tend to be thin, irregular, randomly
- placed or located, strings of materials containing oxygen and reactive elements. Metallic oxide indications can be determined by visual or EDS inspection.
Area | Possible Cause | Potential Correction |
Foundry | Impure melting stock | Use oxide-free melting stock or filters |
Foundry | Oxidation of reactive elements | Prevent oxidation of the melt through the use of vacuum or protective atmosphere |
Foundry | Improper deoxidation practice | Allow time for deoxidation adds to be effective, agitate melt and de-slag for improved deoxidation |
Foundry | Turbulence | Reduced filling speed |
23. Penetration
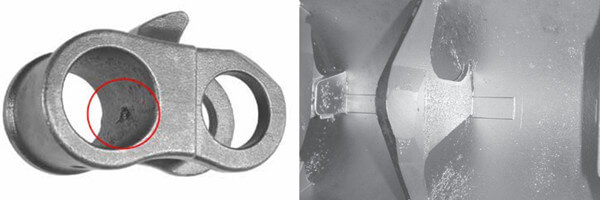
Mechanism
Metal penetrates into the primary layer during casting. Pinholes or air pockets in the primary layer fill with metal during casting OR Stucco penetrates the primary surface and traps an air pocket against the wax.
Description
- Defect Type: Positive
- Appearance: Small discrete positives which appear like grains of sand. When severe, the positives are closely clustered and the surface feels like sandpaper
- Typical Location:Near gates, heavy sections or slow to cool sections of the casting
- Aliases:Burn-in, burn on, pimpling, stucco penetration, rough surface
- Method for defect determination: Visual inspection.
Area | Possible Cause | Potential Correction |
Shell | Stucco particles too large | Change shell code, use finer stucco on the first few shell layers |
Shell | Incomplete slurry mixing | Insure the slurry is completely mixed before using in production |
Shell | Foaming in slurry | Insure air is not being sucked into the slurry by the mixer. Conduct antifoam test and adjust if necessary |
Shell | Primary slurry instability (micro-gelling) refractory solids | Conduct gel test on binder solution. Replace slurry if bad |
Shell | Prime slurry layer too thin | Increase slurry viscosity or reduce slurry drain time. Modify drain orientation. Double dip the mold in the slurry. Increase the pre-wet drain time or orientation |
Shell | Reaction with primary coat contaminants | Ensure rusting or corrosion of the mixing equipment is not occurring. Remove iron contamination with magnets |
Shell | Drain time too long before stucco application | Optimize drain time. Train operators or adjust robot program |
Shell | Rainfall sander too high above pattern | Raise pattern in relation to sand fall |
Shell | Non-uniform sand delivery from rain rainfall equipment | Maintain or adjust equipment |
Shell | Improper air flow in fluid bed | Reduce air flow as needed, keep bed clean. Maintain sufficient flow to avoid having to force patterns into bed |
Foundry | High ferrostatic pressure | Reduce the height of the mold. Reduce the vacuum level. Reduce the spinning speed (centrifugal casting) |
Foundry | Casting cooling rate too slow | Speed up casting cooling, insure cast molds are not too close together. If penetration localized to hot spots, improve radiant heat loss by lengthening gates or increasing the spacing between adjacent parts |
Foundry | Oxidized metal | Improve melting and casting process to prevent oxidationof the melt |
Foundry | Metal temperature too hot | Reduce metal temperature |
24. Pinholes
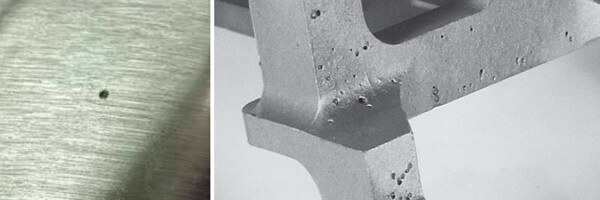
Mechanism
Gases are absorbed in metal during melting. If the gas level in the melt exceeds the solid state solubility limit, bubbles are formed during solidification. The gases most responsible for this defect are hydrogen and nitrogen.
Alternate Mechanism:Chemically combined water in the mold is released by the increase in mold temperature during casting.
Description
- Defect Type: Negative
- Appearance: 1/8” or less
- Size: 1/8” or less
- Typical Location:Dispersed throughout the casting but may be more severe in areas that are last to freeze
- Similar to:Gas, Slag, Incomplete ,Burn-out
- Aliases: Metallurgical gas
- Method for defect determination: Pinhole defects are typically smaller with a higher frequency than gas, slag or incomplete burnout. This defect is more common in plain carbon and low alloy steels than in higher alloy steels.
Area | Possible Cause | Potential Correction |
Shell | Chemically combined water in the mold released duringcasting | Dry the molds completely after autoclave dewaxing. Increase the mold preheat temperature. |
Foundry | High nitrogen, oxygen or hydrogen level in the melt | Use more virgin metal or purchase metal with lower gas content |
Foundry | Dirty, wet or rusty metal | Metal should be clean, dry and free from rust and oils |
Foundry | Wet ladles or pouring spouts | Insure complete heating and dry out of furnace pour spoutsand ladles |
Foundry | Incomplete degassing | Confirm degassing additions are correct |
Foundry | High nitrogen, oxygen or hydrogen level absorption in the melt | Reduce the casting temperature or time the metal is molten. Use a protective or inert atmosphere around melt |
25. Pitting
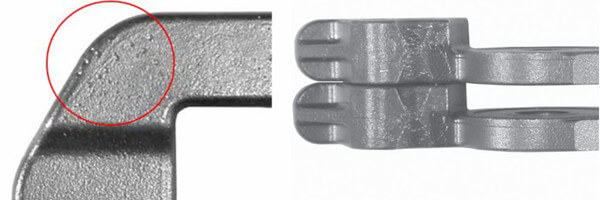
Mechanism
Oxygen reacts with chrome in the metal immediately after casting
Description
- Defect Type: Negative
- Appearance: A multiplicity of dark colored shallow depressions covering a large portion of the casting
- Special Circumstances: Can only occur in high chrome alloys such as 400 series and PH stainless steels
- Typical Location: Thick, slow to cool sections
- Similar to: Gas, Incomplete Burn-out, Slag
- Aliases: Chrome Oxide Pitting, Fusion Spot, Measles
- Method for defect determination:Alloy, number of defect sites, depth of defect
Area | Possible Cause | Potential Correction |
Foundry | Surface oxidation of high chrome-iron alloys | Ensure reducing or inert conditions immediately after casting. Cover the molds after casting. Use carbonaceous materials in or around the mold. Cool in vacuum or protective or inert atmosphere |
Foundry | Lack of carbonaceous material in mold | Reduce mold burnout time or add additional carbon layers during shell building |
Foundry | Casting cooling rate too slow | Increase casting cooling rate |
26. Prime Coat Lift
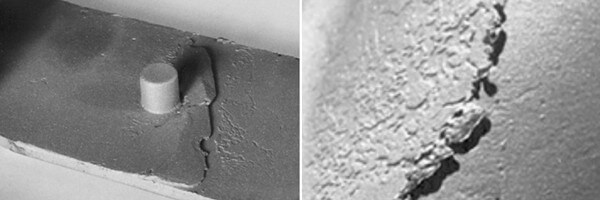
Mechanism
During shell building, the primary coat cracks and lifts off the pattern. Subsequent slurry layers penetrate and fill the gap between the pattern and the primary coat. This defect is a close cousin to buckle.
Description
- Defect Type: Positive
- Appearance: Island of surplus metal often as sociated with flash at the casting edge. The edge of the defect has the appearance of a coastline
- Typical Location: Sharp corners adjacent to flat or featureless surfaces
- Similar to: Buckle
- Aliases: Primary coat buckle, investment penetration
- Method for defect determination: With prime coat lift, the shell also fractures, allowing the backup layers to fill the gap between the primary layer and the wax pattern. When a shell buckles, it only separates from the pattern.
Area | Possible Cause | Potential Correction |
Wax | Wax pattern temperature not stable | Ensure the wax pattern has stabilized in temperature before applying shell layers |
Shell | Poor adhesion of the prime coat to the wax pattern | Increase the etch strength or etch time. Reduce the time from etch to 1st layer application |
Shell | Large temperature drop when applying 2nd layer | Increase the room humidity |
Shell | Large temperature variation during prime coat drying | Maintain +/- 3 F in the dipping and drying area |
Shell | Drying too long | Shorten the dry time |
Shell | Drying too fast (large pattern shrinkage) | Increase the room humidity or reduce airflow |
Shell | Primary coat binder is gelled | Test the primary coat binder to determine if it is gelled |
Shell | Uneven primary,coating thickness giving rise to variable rates of drying | Modify the draining technique to produce a more uniformslurry coverage |
Shell | Slurry dry out on sharp edges | Shorten the draining time,increase the humidity in theshell dipping area |
Shell | Poor adhesion and elasticity properties of the primary slurry | Green strength additives in the primary slurry becoming unstable or ineffective |
27. Rat-tailing
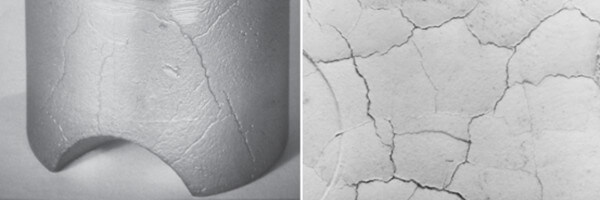
Mechanism
This defect is a marriage of pitting and finning defects. Rat-tailing is the selective oxidation of the metal surface through cracks or micro-cracks in the shell. Most of the cracks are large enough to be filled with metal during pouring and will produce positive metal fins. Very fine micro-cracks are too small to allow metal to enter, but will allow air (oxygen) to reach the hot casting surface.
Description
- Defect Type: Negative with the possibility of positive finning
- Appearance: Shallow rounded threadlike fissures typically in a radial pattern
- Aliases: Mud cracks, drying cracks, oxidation crazing, rivering
- Method for defect determination:Thin, negative defect typically found in high chrome alloys
Area | Possible Cause | Potential Correction |
Other (Set-up ) | Lack of stress raisers on the cast surfaces or in the primary coat refractories | Break-up large flat surfaces on the casting with “hatching” or small ribs which can subsequently be ground off |
Shell | Large temperature variation during prime coat drying | Maintain +/- 3F in the drying area |
Shell | Drying too fast (large pattern shrinkage) | Casting cooling rate too slow. Increase dipping and drying room humidity, reduce air flow |
Shell | Mismatch in expansion coefficient between prime and backup coats | Use slurry and stucco refractories with similar thermal expansion rates |
Shell | Drying too long | Reduce dry time. Cooling rate too slow |
Shell | Low prime coat strength | Check binder healthy/stability through pH, conductivity and/or gel test |
Shell | Low prime coat strength | Increase refractory solids |
Shell | Poor adhesion and elasticity properties of the primary slurry | Green strength additives in the primary slurry becoming unstable or ineffective |
Shell | Uneven shell build on prime coat(s) | Evaluate dipping/draining sequence to ensure uniform draining and/or shell build |
Shell | Permeability of shell is too high | Compare permeability of shell against previous data. If changed, evaluate potential causes for increase |
Foundry | Oxygen level too high during casting cooling | Ensure reducing or inert conditions immediately after casting. Cover the molds after casting. Use carbonaceous materials in or around the mold. Cool in vacuum or protective atmosphere |
Foundry | Oxygen level too high during casting. Casting cooling rate too slow | Casting speed cooling rate too slow |
Foundry | High shell tempera ture and excessive time in oven | Explore potential ways to reduce shell preheat temperature or time |
28. Shot Defect
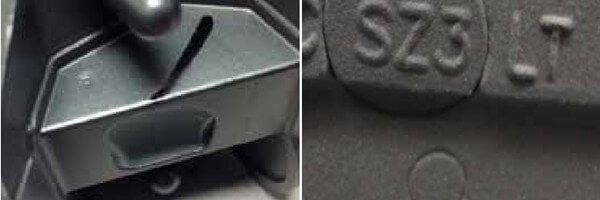
Mechanism
During casting, droplets of metal detach or are separated from the pouring stream by excessive turbulence, mold design, or metal pouring height. The metal droplet becomes either cooler in temperature or coated with a tenacious oxide film and retains this identity as part of the cast metal.
Description
- Defect Type:Negative
- Appearance :These are closely related to oxide fold defects but are typically circular in form rather than linear
- Size: Can be small up to an inch or more in diameter
- Typical Location:Generally located on the surface of the casting
- Similar to: Wax flow lines (See Atlas of Wax Pattern Defects)
- Aliases: Oxidized droplet
- Method for defect determination:Visual or Fluorescent Penetrant Inspection.
Area | Possible Cause | Potential Correction |
Wax | Cold wax at nozzle tip | Wax cold shot can occur in the wax pattern and be duplicated through the shelling process, thereby resulting in a similar-looking metal defect. (Ensure nozzle tip temperature is adequate to keep wax from solidifying). |
Other (Mold design) | Bad mold design | Mold design should promote non-turbulent metal flow |
Foundry | Bad pouring practice | Avoid metal splashing during pouring |
Foundry | Bad pouring practice | Reducing the distance between the crucible and the mold to be poured to minimum, thereby reducing the chance for splashing |
Foundry | Pouring practice | Employ use of a reticulated foam filter to achieve a laminar flow |
Foundry | Pouring practice | Formation of a well in the mold to allow the metal to collect and then flow into the mold parts |
29. Shrink – Gate
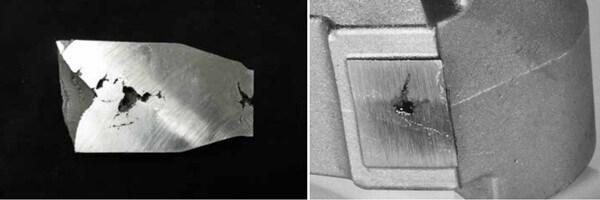
Mechanism
The molten alloy shrinks as it solidifies. Inadequate feed metal from the gating system is available to prevent a cavity from forming.
Description
- Defect Type: Negative
- Appearance : Internal irregular cavity exhibiting an open or porous coarsely crystalline or dendritic structure usually exposed upon removal of the gate. This defect is frequently discovered by caustic salt bleed out from the cavity
- Typical Location: Center of gates
- Similar to: Shrink – Surface, Shrink – Internal
- Method for defect determination: Visual inspection, Penetrant Inspection
Area | Possible Cause | Potential Correction |
Other (Gatingd esign) | Gates are too small or too long | Increase height of mold to increase ferrostatic pressure or the gate modulus, consider tapering the gate |
Other (Casting design) | Low metal pressure | Insulate, hot top or use exothermic material to prevent the pour cup from freezing too early |
Foundry | Runner system freezing too early | Use selective insulation to promote progressive solidification |
Foundry | Gates are too small or too long | Increase height of mold to increase ferrostatic pressure or the gate modulus, consider tapering the gate |
30. Shrink – Internal
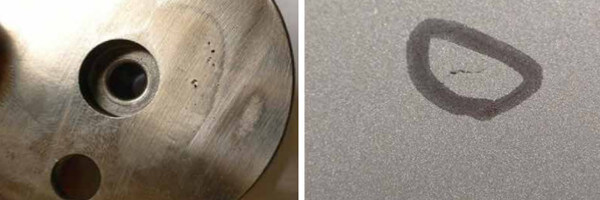
Mechanism
Molten alloys shrink as they solidify. As solidification progresses and the solid to liquid fraction increases, it becomes more difficult for liquid feed metal to reach the solidification front. Shrinkage occurs between dendritic arms. In larger defects, inadequate feed metal is provided to isolated hot spots in the casting.
Description
- Defect Type: Negative
- Appearance: Internal irregular cavities ranging from small dispersed or linear type cavities up to large cavities
- Special Circumstances: The occurrence and severity of this defect may be alloy dependent. Alloys with longer (larger) freezing ranges are more prone to this defect.
- Size: Shrinkage cavities can range in size from very small (requiring magnification) to very large
- Typical Location: Casting centerline between gates or in isolated heavy sections. Areas with sharp internal corners
- Similar to: Shrink – Gate, Shrink – Surface
- Aliases:Dendritic shrink, micro-shrink
- Method for defect determination: Because this is a subsurface defect, if may not be discovered without x-ray examination, machining or sectioning through the casting.
Area | Possible Cause | Potential Correction |
Other (Mold design) | Inadequate or incorrect feeding | Ensure adequate feeding of the area concerned to promote progressive solidification |
Other (Mold design) | Incorrect solidification rate | Modify the casting design to promote progressive solidification |
Other (Mold design) | Vacuum in blind riser | Ensure the v-notch in the riser prevents a vacuum from forming |
Other (Mold design) | Blind riser too small | Ensure the riser has adequate metal volume |
Other (Mold design) | Low ferrostatic head pressure | Increase the height of the mold. Use centrifugal force to increase head pressure |
Other (Mold design) | Incorrect solidification rate | Examine the molding technique. Modify the casting design to promote progressive solidification. |
Foundry | Incorrect casting conditions | Establish the correct casting conditions |
Foundry | Incorrect solidification rate | Use insulation on specific areas of the mold to increase thermal gradient |
Foundry | Low metal temperature | Increasing the metal temperature can improve the feeding distance |
Foundry | Low mold temperature | Increasing the mold temperature can improve feeding distance |
Foundry | Vacuum created in the feeding system during solidification | Ensure the metal in the head (pour cup) remains liquid longer than the casting. Insulate or use exothermic material on the pour cup and risers |
Foundry | Dissolved gas level too high | Use a heat makeup and melting practice that produce low dissolved gases |
Other (Casting Processing) | Inadequate or incorrect feeding | Use hot isostatic pressing (HIP) to close up the defects. Cap weld all surface connected shrinkage prior to HIP. |
31. Shrink – Surface
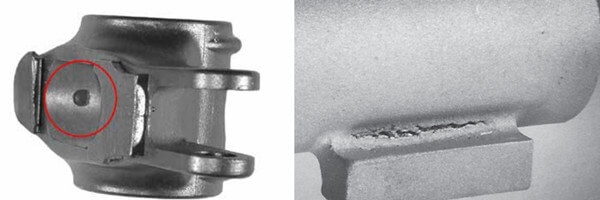
Mechanism
The molten alloy shrinks as it solidifies. Sharp inside corners thermally saturate the shell and cool slower than the surrounding area. Unfavorable thermal geometry resulting in an isolated liquid metal heat center. The shrinkage of the internal section, cut off from supplies of further liquid feed metal, causes atmospheric pressure to collapse the adjacent skin where the metal is still sufficiently hot and weak to do so.
Description
- Defect Type: Negative
- Appearance: Surface depression or irregular cavities exhibiting an open or porous or coarsely crystalline structure sometimes exhibiting a dendritic appearance. These defects are frequently discovered by caustic salt bleeding out of the cavity after the leaching.
- Typical Location: Fillets, sharp intersections. or slow and are commonly found at corners of castings near the ingate.
- Similar to: Shrink – Gate, Shrink – Internal.
- Aliases: Hot spot porosity.
- Method for defect determination: Visual and Penetrant inspection.
Area | Possible Cause | Potential Correction |
Wax | Fillet too small | Increase fillet size |
Wax | Inadequate feeding.Castings too close together – localized mold hot spots | Ensure adequate feeding. Improve pattern spacing and avoid refractory build-up in completing molds. |
Foundry | Metal pouring temperature too hot | Consider reducing temperature |
Foundry | Mold temperature too hot | Consider reducing temperature |
Other (Metal/ Mold design | Differences in radiant cooling. | Review the assembled mold. Is the defect related to a specific position on the mold? |
Other (Casting design) | Fillet too small | Increase fillet size |
Other (Mold design) | Inadequate feeding. Castings too close together – localized mold hot spots | Ensure adequate feeding. Improve pattern spacing and avoid refractory build-up in completing molds. |
32. Sink
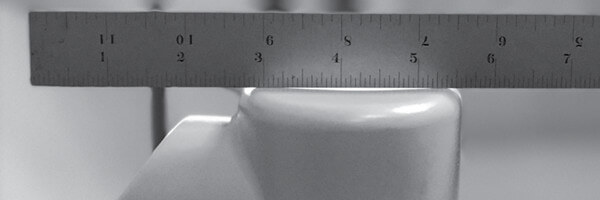
Mechanism
Heavy section of wax pattern shrinks as it cools. The vacuum created during cooling causes the surface to cavitate or dish inward.
Description
- Defect Type: Negative
- Appearance: Smooth, dished surface depression
- Size: varies
- Typical Location: Heavy sections or thick flat surfaces
- Similar to: Wax Shrink (See Atlas of Wax Pattern Defects)
- Aliases: Cavitation
- Method for defect determination: Visual inspection, overlay of straight edge or customary dimensional inspection tools.
Area | Possible Cause | Potential Correction |
Other (Wax Tool Design) | Feed runner freezing prematurely | Increase size or add runner to affected section |
Wax | Incorrect wax injection parameters | Reduce wax temperature, increase injection time, increase injection pressure |
Wax | Missing wax chill | Create wax chill to reduce the volume of injected wax in the area of sink/cavitation |
Wax | Hot wax chill | Allow time for the wax chill to cool to room temperature before inserting in the wax injection die |
33. Slag
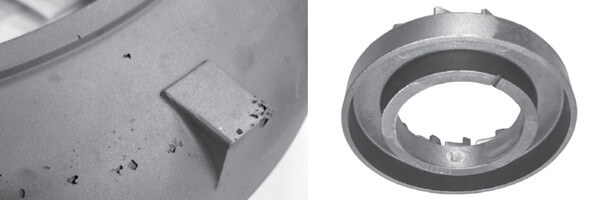
Mechanism
During melting or casting, slag is produced as a function of time, temperature and availability of oxygen. This slag is mixed with the metal during pouring and, being less dense than the metal, floats to the top surface of the casting.
Description
- Defect Type: Negative
- Appearance : A series of smooth-walled symmetrical surface cavities with or without traces of dark glassy included material
- Typical Location:Top surface of the casting as oriented at casting
- Similar to:Gas, Pinholes, Incomplete Burn-out
- Method for defect determination:It is difficult to visually distinguish between slag and gas defects. The defect shapes are similar as is the location. Inspection of the defect under magnification may reveal residual slag.
Area | Possible Cause | Potential Correction |
Shell | Metal / mold reaction | Cast at the lowest possible mold and metal temperature. Increase the refractoriness of the primary coat |
Foundry | Crucible / metal reaction | Employ correct crucible and melting practice |
Foundry | Oxidation of furnace lining or ladle | Change to more refractory material |
Foundry | Poor or improper deslagging practice | Ensure adequate slag removal at the lowest possible temperature. Allow time for slag in melt to float out. Remove slag. Use slag coagulants if necessary to improve removal. |
Foundry | Excessive superheat temperature and or holding times | Minimize the time the metal is at temperature |
Foundry | Oxidation of metal during melting | Consider protecting the melt using inert gas |
Foundry | Silicates formed during deoxidation | Modify the deoxidation practice |
Foundry | Slag from the ladle entering the mold | Use ceramic or cloth filter |
Foundry | Slag from ladle entering the mold | Consider using a bottom pour (teapot) ladle |
Foundry | Turbulent pouring conditions – metal poured from great height above molds | Minimize the distance from the furnace / ladle to the mold |
34. Slurry Leakage
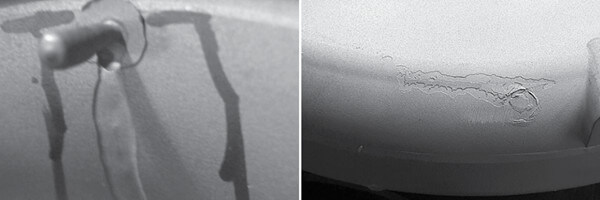
Mechanism
Liquid ceramic slurry enters the mold and dries creating a positive in the mold that is represented as a negative in the casting.
Description
- Defect Type: Negative
- Appearance: Shallow, irregular depression in casting surface
- Size: varies
- Typical Location: Near wax vent or in mold crack
- Method for defect determination: Visual inspection.
Area | Possible Cause | Potential Correction |
Shell | Damage to coating creates separation from wax passage for slurry entry | Awareness/Handling |
Other (Mold Preparation) | Inadvertent spill | Awareness/Cleanliness |
35. Spall
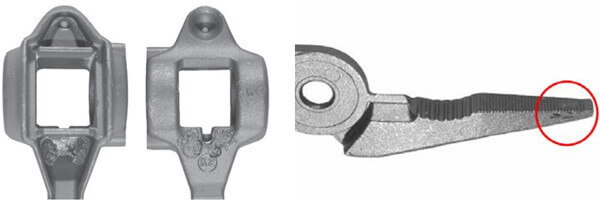
Mechanism
The layer to layer bond in the shell construction is not strong enough and the ceramic fractures off the mold surface during dewaxing, mold preheating or casting and falls into the mold cavity
Description
- Defect Type: Positive (with corresponding negative)
- Appearance: Sharp or irregular positive defect normally accompanied by a negative defect (inclusion) from the ceramic that has “spalled” off and appears somewhere else on the casting.
- Typical Location: Detailed areas such as depressed lettering, score lines, teeth, tight slots, fillets or sharp corners
- Similar to: Penetration (positive), Non-Metallic Inclusions (negative)
- Aliases: Spalling, prime coat spall, pre-coat spall, undercuts
- Method for defect determination: Visual Inspection
Area | Possible Cause | Potential Correction |
Shell | Excessive 1st layer slurry that results in weak inter layer shell construction | Fully drain slurry coats |
Shell | Incomplete 1st layer dry that results in weak inter layer shell construction | Extend prime slurry dry time |
Shell | Excessive pre-wet that results in weak inter layer shell construction | Fully drain pre-wet to matte finish |
Shell | Prime coat stucco too fine that results in weak inter layershell construction | Skim fines/dust from the fluid bed or screen out, use coarser stucco |
Shell | Low primary slurry binder level | Check SiO2 level of primary slurry |
Shell | Prime slurry binder gelling | Conduct gel test on primary slurry binder |
Shell | Poor stucco adhesion | Insure the slurry is not drying before stucco,eliminate stucco rub off, blow off loose stucco |
Shell | Prime coat slurry too thick | Reduce prime coat viscosity |
Shell | Etch too strong | Reduce etch time, etch strength or increase time from etch to 1st layer application |
Shell | Thermal expansion mismatch | Use refractories that have similar thermal expansion characteristics |
36. Stuck Shot
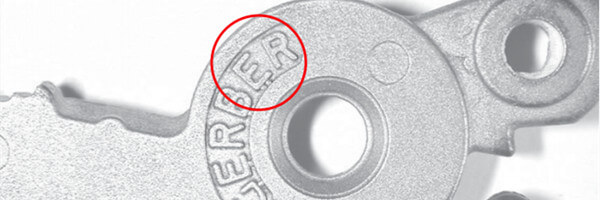
Mechanism
Shot wedged into lettering or detailed areas during shot blasting operation
Description
- Defect Type: Positive
- Appearance: Smooth – round, oval, or hemispherical
- Special Circumstances: Can only occur in areas of the casting that shot can get wedged into
- Size: 1/8” or less
- Typical Location: Highly detailed areas such as depressed lettering or score lines
- Similar to: Wax bubbles (See Atlas of Wax Pattern Defects), Bubbles
- Aliases: Positive metal
- Method for defect determination: Stuck shot can be pried out. Can also section, mount and polish through defect. Stuck shot will not be attached to the casting – only wedged in place.
Area | Possible Cause | Potential Correction |
Other(Shot blast) | Shot is the wrong size for the part | Change the shot size |
37. Wax Drip
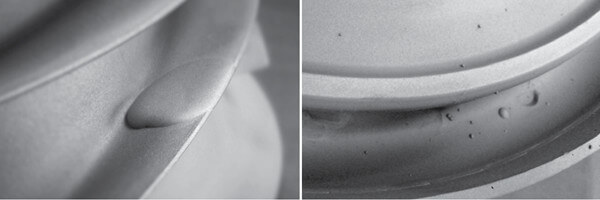
Mechanism
Molten Wax or sticky wax drips onto the pattern during gating assembly process
Description
- Defect Type: Positive
- Appearance: Smooth. Spherical or oval shaped sometimes accompanied with a tail.
- Typical Location: Exposed surface during gating
- Aliases: Wax Splatter
- Method for defect determination: visual
Area | Possible Cause | Potential Correction |
Wax | Wax melting iron / torch too hot | Reduce temperature |
Wax | Sticky wax too hot | Reduce to correct temperature |
Wax | Poor gating technique | Use a shield (aluminum foil) to prevent drips from getting on the pattern |