Valve Casting Foundry
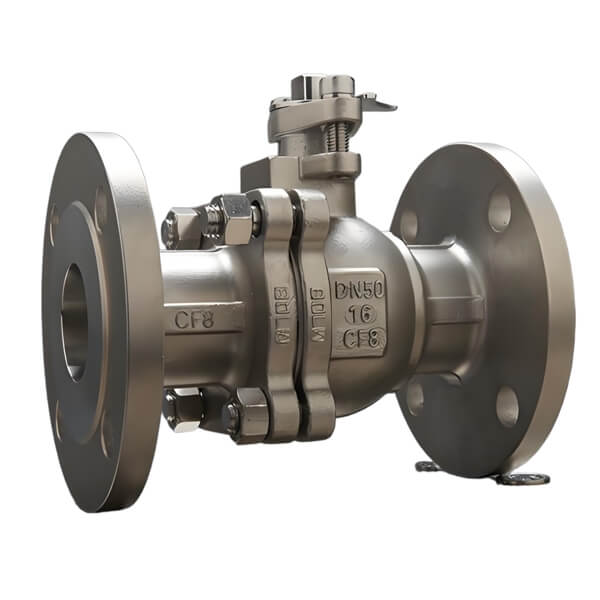
JC Casting is a leading manufacturer specializing in valve castings, supported by its own dedicated foundry. Valves are essential components in industrial pipeline delivery systems, responsible for controlling the flow, direction, and pressure of various media. JC Casting produces a wide range of valve castings, with sizes ranging from as small as one cubic inch to large dimensions of 18 inches long by 18 inches wide by 8 inches high, and weights varying from 1.5 ounces up to 50 pounds. This extensive range allows JC Casting to meet diverse industrial needs with precision and reliability.
Benefits of Valve Castings
- Design flexibility:The valve castings shapes can be designed flexibly
- Wide materials selection. Castings allow you to choose from many alloys as well as have the flexibility for internal and external configurations to suit your particular needs.
- Less expensive secondary operations by choosing an optimal casting process.
- Elimination of material waste. valve castings are cast to size.
Valve Casting Process
- Sand Casting
- Lost Wax Investment Casting
- Lost Foam Casting
The company’s valve casting process utilizes advanced techniques such as sand casting, lost wax investment casting, and lost foam casting. Their green sand-molding method involves creating heat-activated resin-coated sand cores to form the internal passages of the valves, followed by automated molding and precise pouring of molten metal. This process ensures high-quality valve castings with excellent dimensional accuracy and structural integrity.
Types of Valve Castings
JC Casting offers a variety of valve types including check valves, gate valves, globe valves, foot valves, pressure relief valves, ball valves, and various valve components like poppets, strainers, and washers. Each product is designed to fulfill specific functions such as cutoff, throttling, regulation, diversion, and overflow relief, making them indispensable in fluid control systems.
- Check valves: Consist of two openings in the valve body; one for fluid to enter and the other for fluid to exit. These are used in a wide variety of applications.
- Gate Valve Casting
- Globe Valve Casting
- Foot valves: A form of check valve, installed at the bottom of a pump suction line inside of a wet well.
- Pressure relief valves: Safety valves used to control or limit the pressure in a fluid system.
- Valve components – Such as poppets, strainers, and washers used to regulate and control fluid flow.
- Ball valves: This valve controls the flow of liquids using a rotary ball.
Difference Between Valve Casting and Valve Forging
Valve forging and valve casting are the two primary casting methods of creating metal valves. The main difference between casting and forging is in the way the metals are shaped. While valve forging involves shaping the metal into the desired form while the metal is still solid, valve casting involves pouring liquid metal into a mold of the valve.
One of the key advantages of valve casting over forging is the ability to create complex shapes with design flexibility and reduced material waste, as castings are made to size. JC Casting also provides a wide selection of materials to suit different operational requirements, including stainless steels (EN10213, AISI 304/316 series), ASTM grades, brass, and bronze. Material selection is carefully considered based on factors like strength, corrosion resistance, machinability, and thermal properties.
Valve Casting Materials
Valve Casting Materials selection elementor need to consider as belows:
- cost, strength, hardness,
- density weight limitations,
- bearing qualities
- galling resistance,
- machinability, weldability,
- abrasion resistance,
- corrosion resistance,
- oxidation resistance,
- fatigue properties,
- resistance to cracking,
- electrical conductivity,
- magnetic properties,
- thermal conductivity
The common Valve Casting Materials in JC Casting foundry
- EN10213:1.4308, 1.4408, 1.4309,1.4409, 1.4581, 1.4469, 1.0619, 1.6220, 1.4308, 1.4408, 1.4581
- AISI: 304,304L,316,316L
- ASTM A351: CF3,CF3M,CF8,CF8M
- ASTM A743: CG3M
- ASTM A995: 5A
- ASTM A216: WCA,WCB,WCC
- Brass and bronze
Your Valve Casting Manufacturer China
With its comprehensive production capabilities, experienced team, and commitment to quality, JC Casting stands out as a reliable valve casting manufacturer in China. Their expertise ensures that customers receive durable, cost-effective valve castings tailored to their specific industrial applications.