What is investment casting
Investment casting, also known as lost wax casting or investment casting. It is a method of precision casting by using wax molds. The basic principle is to create an accurate model using a fusible material such as wax. The surface of the model is then coated with multiple layers of refractory paint. After drying and hardening, a shell is formed. The wax mold is melted by heating,then leave a cavity. The shells are then roasted at high temperatures to increase strength and remove residual impurities. Finally, the molten metal is poured into the shell. After cooling, the casting is obtained.
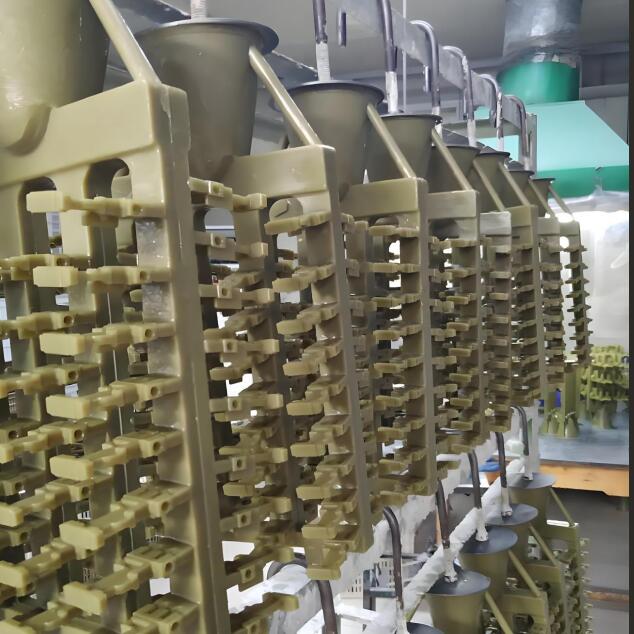
Table of Contents
Investment Casting Process
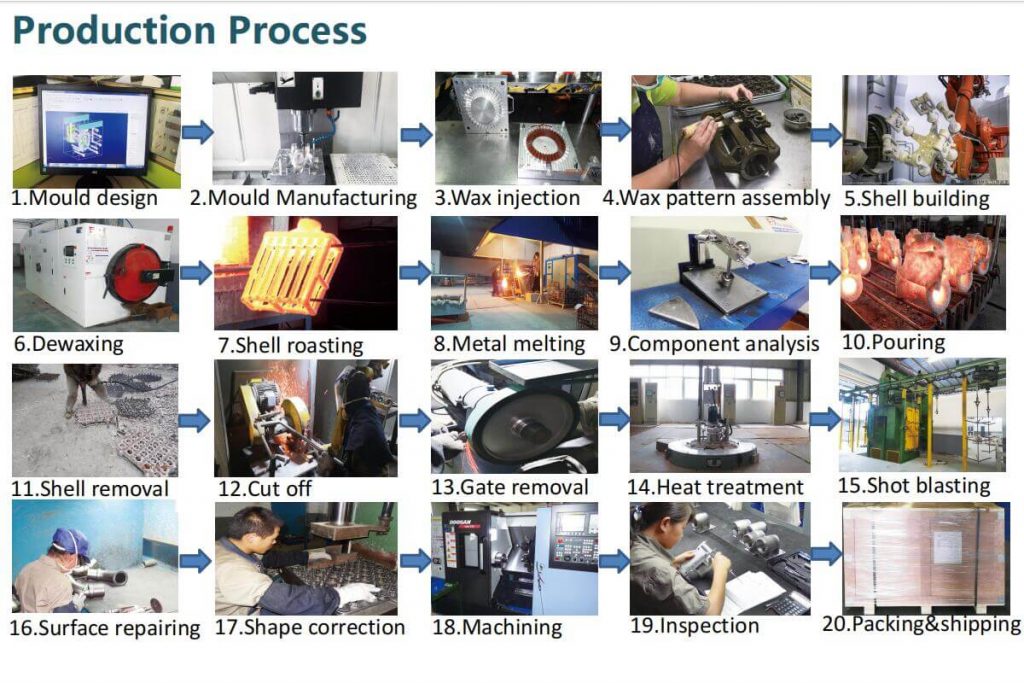
Step 1: Making the wax pattern
The production process begins with the creation of the wax model. Wax models are usually made by injecting molten synthetic wax into a steel or aluminum mold. After the wax mold was finished. The individual wax patterns are attached to a wax “tree”. Multiple patterns can be attached to the wax “tree” to produce multiple parts simultaneously.
Step 2: Ceramic Shell making (Mold Formation)
With the wax tree ready, it’s dipped into a ceramic slurry. Coated with fine refractory sand. Then coats Coarser ceramic sand. The dipping – sanding process repeats 4 – 8 times. Each layer needs time to dry. After several days, a multi-layer ceramic shell forms.
Step 3: Dewaxing
The ceramic-coated wax tree is heated in a dewaxing furnace to 800°F – 1200°F (427°C – 649°C). Melting can make the wax out and leave a hollow ceramic mold.
The wax melts and flows out through pre-designed vents. Precise temperature and time control are crucial to avoid shell damage. Ensure all wax is removed, leaving a hollow ceramic mold.
Step 4: Metal Pouring
Molten metal (such as steel, aluminum, titanium, or bronze) is poured into the hollow ceramic mold.The molten metal is quickly and steadily poured into the ceramic mold to fill it completely. And avoid air bubbles. Cooling and solidifying can take 30 minutes to several hours.
Step 5: Shell Removal and Finishing
The ceramic shell is broken away after the metal cools and solidifies. The cast parts are cut from the tree, cleaned, and finished (machining, polishing, etc.).
For a more detailed look at the precision casting process, please refer to the 11 steps of investment casting proesses
Investment Casting Materials
The investment casting process is extremely flexible. It can work with many types of metals and alloys. Below are some of the metals that are most commonly used in investment casting
Metal Type | Representative Models | Introduction | Application |
Stainless Steel | 304, 316, 17-4 PH, 2205 duplex, etc. | With high strength, good corrosion resistance, and machinability, stainless steel is an excellent choice for investment casting. | Marine Hardware, Pipe Fittings, Automotive Components, Glass Fittings, Etc. |
Carbon Steel | AISI 1020, AISI 1030, AISI 1045, etc. | A common material for investment casting, with good mechanical properties. | Automotive Components, Industrial Equipment, And Construction |
Alloy Steel | AISI 4140, AISI 8620, AISI 8630, etc. | With a good balance between strength and toughness | Bucket Teeth |
Nickel-Based Alloys | Inconel, Hastelloy, etc. | Have excellent heat resistance and corrosion resistance. Due to the high nickel content, the cost of nickel-based alloy castings is much higher than that of stainless steel castings. | Used In Special Environments That Require High Corrosion Resistance Or High Heat Resistance. |
Aluminum Alloys | A356, | lightweight, strong, and corrosion-resistant. easy to cast. good thermal and electrical conductivity. | In Automotive And Aerospace |
Copper Alloys | Bronze, brass | Good corrosion resistance, thermal conductivity, and aesthetic appeal. | Valve |
Titanium Alloys | None specifically listed | high strength, low weight, and corrosion resistance | Aerospace And Medical Industries. |
Precious Metals | Gold, silver, etc. | Nice surface, good looking and complex design | Decoration Parts |
Investment casting applications
Advantages and Disadvantages of Investment Casting
Advantages of Investment Casting
✔ High Precision – Can produce complex shapes with tight tolerances (±0.005 in or better).
✔ Smooth Surface Finish – Reduces the need for extensive machining.
✔ Wide Material Compatibility – Works with almost any metal (stainless steel, superalloys, aluminum, etc.).
✔ Thin-Wall Capability – Can produce very thin sections (as low as 0.015 in).
Disadvantages:
❌Higher Cost– More expensive than sand casting due to wax and ceramic mold materials.
❌ Size Limitations– Typically used for small to medium-sized parts (usually under 50 lbs).
2 Types of Investment Casting
There are two primary investment casting processes: silica-sol investment casting and water glass investment casting.Each of them has its individual benefits and distinctive features.
Silica-sol Investment Casting
This is a type of investment casting (lost wax method). Silica sol (SiO₂ colloidal solution is used as the binder. High-precision shells are prepared by coating refractory materials. (For Example: corundum sand, mullite sand) layer by layer. After drying, dewaxing and high-temperature roasting, the shell forms a hard ceramic shell. Used for casting stainless steel, high temperature alloy, aluminum alloy and other metal liquids. Complex castings with smooth surfaces and high dimensional accuracy are obtained.
Core features: Dependent on the gelation characteristics of silica sol to form a high-strength shell. Suitable for high-precision, complex structure castings.
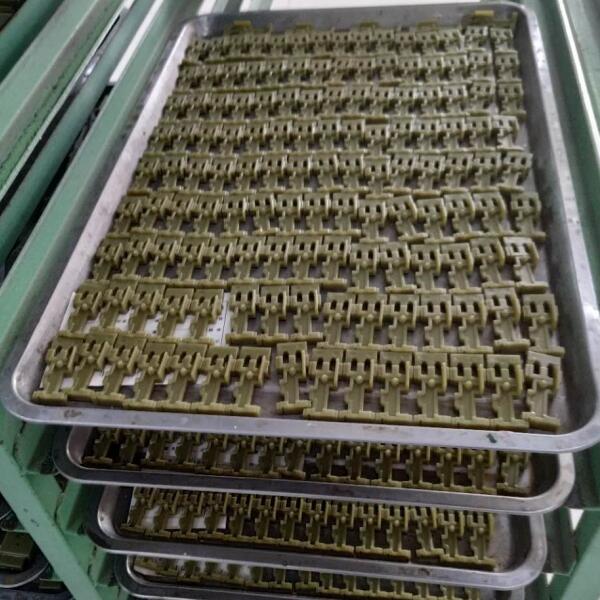
Water Glass Investment Casting
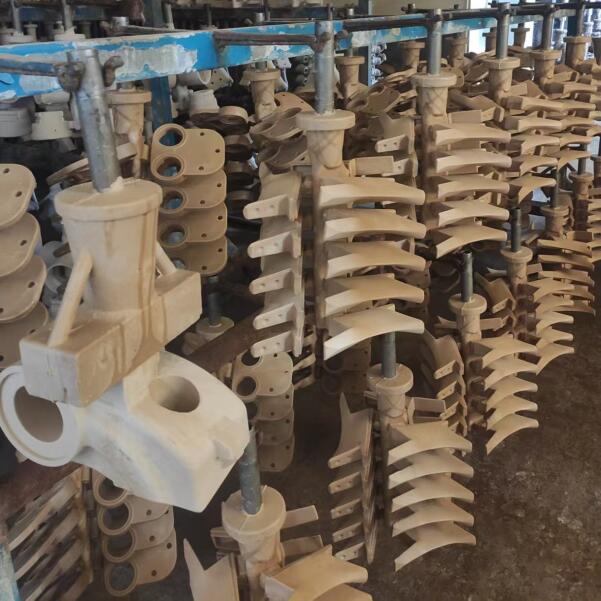
Also belongs to the principle of investment casting. Water glass (sodium silicate aqueous solution, Na₂O・nSiO₂ as a binder. By coating refractory materials. (Such as quartz sand) and reacting with hardeners (such as ammonium chloride, magnesium chloride). Rapid curing of the shell. Commonly used in carbon steel, low alloy steel, copper alloy and other castings production. Suitable for scenarios with medium requirements for precision and surface quality.
Core features: The use of water glass and hardener chemical reaction to achieve the hardening of the shell. Lower cost but limited precision.
Compared with other Casting Process
When choosing the manufacturing method for casting, we have to evaluate multiple factors. Design complexity, dimensional accuracy, surface finish requirements, material compatibility, cost-efficiency, production scale, tooling complexity, weight range, and the ability to reproduce intricate details. The following table compares investment casting with sand casting, die casting, CNC machining/Pringting with a focus on the distinct advantages of investment casting.
Process | Precision (mm) | Surface Roughness (Ra) | Suitable Materials | Typical Cost |
Investment Casting | ±0.05 – 0.1 | 1.6 – 3.2 μm | All Metals | High |
Sand Casting | ±0.5 – 1.0 | 12.5 – 25 μm | Cast Iron, Aluminum | Low |
Die Casting | ±0.1 – 0.2 | 0.8 – 1.6 μm | Aluminum, Zinc, Magnesium | Medium – High |
Metal 3D Printing | ±0.02 – 0.1 | 5 – 15 μm | Titanium, Nickel-based Alloys | Extremely High |
When to Use Investment Casting
Precision casting is a casting process with less or no cutting. It is capable of obtaining castings with high dimensional accuracy and surface quality. The following are some of the situations to choose investment casting
Complex shaped parts When the part has a complex shape, internal structure or fine details. Precision casting is ideal. For example, the impeller of an aircraft engine.
High precision requirement parts The parts with very high requirements for dimensional accuracy and surface quality. Such as the cylinder block and cylinder head of automobile engines. Precision casting can meet the tolerance requirements to ensure the assembly accuracy and performance of the parts.
High melting point alloy parts In the manufacture of high melting point alloys. (Such as nickel-based alloys, titanium alloys, etc.) parts. As these materials are difficult to mold through machining. Precision casting can realize the manufacture of complex shapes at a lower cost. For example, in the aerospace industry, many high-temperature parts are made from precision cast titanium alloys.
Mass production of parts Investment casting is suitable for small to medium to large production runs. Once the mold is made, a large number of identical parts can be produced efficiently. And the quality is stable and the production efficiency is high. The cost is relatively low. For example, mechanical standard parts, connectors.
Parts with high appearance requirements for some parts that require good appearance quality. Such as jewelry, art, medical equipment. Precision casting can realize fine surface texture and smooth surface. Reduce the workload of subsequent grinding and polishing.
Investment Casting Company —JC Investment Casting Foundry
JC Casting Foundry is one of the leading investment casting companies in China. With rich experience, we provide high-quality investment casting solutions for various industries. Especially the Castings with high difficulty level, high precision and complex structures.
Our Capabilities of Investment Casting
Design Services
We have a group of experienced engineers and designers. We will communicate with you 1 to 1. We will design an exclusive casting program according to your needs. In this process, we will fully consider the practicality and performance of the castings. Let the design more close to the actual use. We also use the most advanced CAD, CAM design software.Improve the design accuracy and also speed up the design.
Mold Manufacturing
A good mold is the basis for producing high quality castings. Only if the molds are made accurately, the castings can be produced with precise dimensions and high quality.The mold manufacturing equipment in our factory are the top in the industry. When manufacturing molds, we use a variety of advanced techniques and tools. Every detail is carefully carved. Just to make molds with high precision and stable quality.
IInvestment Casting Process
We use silicone sol lost wax casting process. We specialize in overcoming the production problems of complex and fine castings. No matter how complex the structure of the castingHow complex.We can through the precision casting technology. Strictly control the size tolerance.Can also make the casting surface smooth and flat.The casting surface is smooth and even, and the quality standard is very high.Each casting can stand the test.
CNC Machining
In order to let you get your hands on the direct use, we also provide machining services. From milling and turning to drilling and tapping, the machining is highly accurate.We can process the casting parts into perfect finished products according to your requirements.No need for you to do secondary processing.
Surface treatment
Castings are not only good for use, but also important for appearance. That’s why we offer a wide variety of surface treatments.Polishing sandblasting, powder coating and so on.All of our skilled workers can make the casting face value and performance double enhancement.
Quality Inspection
From the beginning of investment casting to the final product, we have set up strict quality inspection barriers at every stage. We have a professional quality inspection team and testing laboratory. Each piece of casting is inspected and various performance tests are conducted. Only if it fully meets the standard, it will be shipped out of the factory.
Packaging and Delivery
Our exclusive packaging solutions protect the castings from damage during transportation in the most secure way. Our global logistics network is fast. We also track the whole process. Delivery is guaranteed on time, without delaying the progress of your project.
Work with Us on your Project!
Briefly describe what the form is for or provide additional context if required. Use inviting language.